Electrical enclosures: Protecting your equipment, system, process and people
- Like
- Digg
- Del
- Tumblr
- VKontakte
- Buffer
- Love This
- Odnoklassniki
- Meneame
- Blogger
- Amazon
- Yahoo Mail
- Gmail
- AOL
- Newsvine
- HackerNews
- Evernote
- MySpace
- Mail.ru
- Viadeo
- Line
- Comments
- Yummly
- SMS
- Viber
- Telegram
- Subscribe
- Skype
- Facebook Messenger
- Kakao
- LiveJournal
- Yammer
- Edgar
- Fintel
- Mix
- Instapaper
- Copy Link
Posted: 25 November 2017 | Christian Westwood (Rittal Limited) | No comments yet
There are a myriad of different processes in our airports today and one that’s critical to both passenger safety and experience is baggage handling. But how can operators optimise the service life of these systems to help ensure they are fully functional in decades to come? Christian Westwood, Industry Manager at Rittal Limited explores.
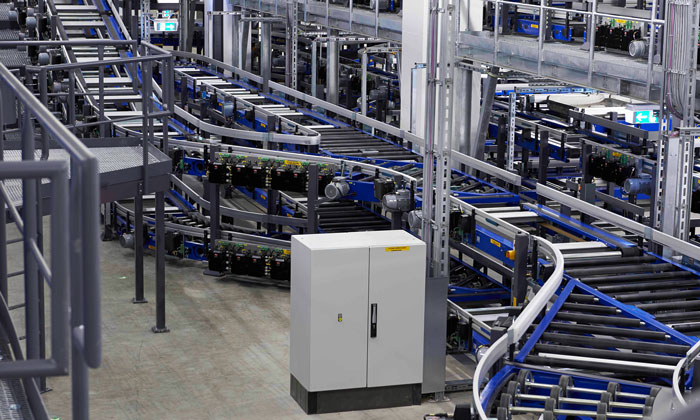
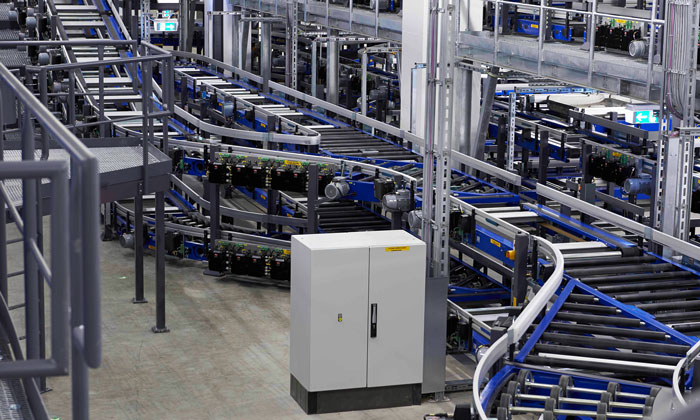
Increased passenger numbers means sorters need updating to ensure they cope with demand
Systems that automate the baggage handling process have been in place for many years. The demands made on these systems are constantly growing, with both the functions they’re required to perform and the number of people using air travel, increasing over time.
Although the main purpose of a baggage handling system is the movement of luggage, a typical scheme will carry out many other tasks that serve to ensure luggage is delivered to where it needs to be, when it needs to be there. Sorting is just one of these tasks, involving the identification of individual bags as well as the information associated with them and directing them around the system accordingly.
But there are many systems that have been in place for decades – some baggage handling systems have been running continuously for at least 25 years. Furthermore, if the annual number of passengers carried globally is analysed for this same period, this has risen more than three-fold, from 1. 145 billion in 1992 to 3.696 billion in 2016.
The increase in passenger numbers is one of the reasons that it may be deemed necessary to bring sorters in a baggage handling system up-to-date. Older systems typically have speeds of 1. 5 m/s whereas newer ones can run at 2. 0 m/s, meaning more bags can be sorted in any given time period. Given that passenger numbers are at an all time high and connection times are under continuous pressure to be reduced, a more efficient baggage handling system as aforementioned, which is 33 per cent faster, could be the difference between a good passenger experience and a great one.
There is also the question of the cost of staying still. For example, the potential cost of a system that may not be as reliable as it was in its prime? Or the true cost of downtime for a baggage handling system? Or the impact of a process stopping without warning not just at that airport, but also at other airports through the knock-on effect of any disruption and delays?
Other costs may be more easily quantified – for example, how much is spent on maintaining aging baggage handling systems and mitigating the risk of system failure? This latter point may be another reason to invest in a replacement system; the cost of maintenance for a new system will inevitably be far less than for one that is 25 years old.
It says something about these earlier systems however, that they’re still operating today.
Optimising service life
How can operators optimise the service life of the new sorters to help ensure they are also fully functional in decades to come?
Providing the optimum conditions for the safe and continued operation of the sensitive electrical and electronic equipment used to monitor, control and automate the sorting process should surely be considered essential.
An enclosure, put simply, is a closed housing, with access that creates a protective environment for installed equipment at a specified location. Don’t let descriptions be deceptive, however, as the long-term operation of large and complex systems are very often dependent on these seemingly modest components. There are many factors to consider when selecting an enclosure suitable for a particular application, however the protection afforded to installed equipment, the durability of the product in what may be a harsh environment, long-term reliability and the flexibility to modify or add to a bayed suite are crucial factors which should underpin any decision.
The protection requirements for system enclosures varies according to installation site, sector and application and these are set out in standards and regulations, some of which are generic and some of which are industry-specific. The most well known classifications for the protection against ingress of particulates and moisture for enclosures are the ingress protection (IP) categories defined in IEC 60529. It should be noted that additional certifications are required for certain markets (North America, Europe or Asia, for example). In North America, NEMA standards or UL certifications are needed for the verification of protective functions instead of IEC standards.
For certifications from organisations such as UL, production facilities are checked regularly following the initial assessment. If the audit is successful, these classification bodies grant permission for their seal of approval to be used on the enclosures until the next inspection. Manufacturers that are certified by these organisations can therefore be relied on to provide enclosures of a consistent quality.
Alongside regular quality tests, a standardised production process is also important to ensure items of a consistent quality are manufactured and supplied. Such a process, when used in conjunction with a platform or modular approach to design and fabrication, ensures the same standard is maintained for bespoke or non standard products as the essential building blocks remain the same. Special enclosures are therefore produced and finished in the same way and do not differ in terms of quality from products stocked as standard.
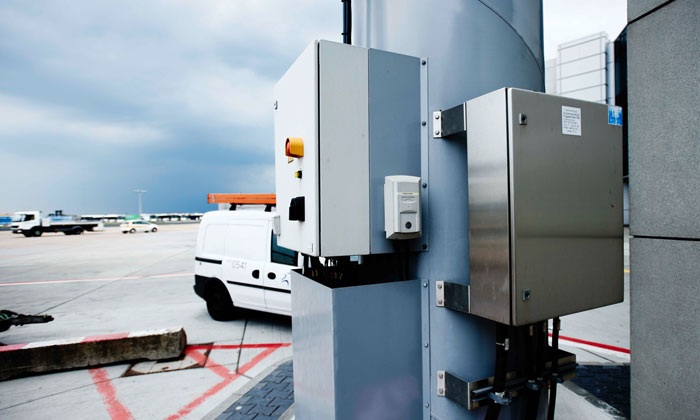
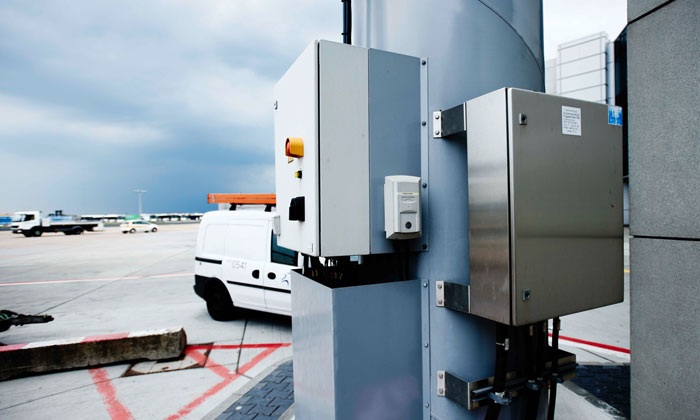
Essential thinking: safe housing of electrical equipment that operates baggage sorting processes
A top-quality enclosure makes use of the latest technology and fulfils the requirements set out in the relevant standards. For instance, long-lasting corrosion protection, which is paramount for electrical enclosures to provide protection for both personnel and equipment even after many years in operation, involves more than just a layer of paint across the metal body. Ensuring long-lasting corrosion protection requires a specific process made up of several different stages, from initial cleaning to a final powder-coating of the primed enclosure.
It’s possible for spray-finished sheet steel enclosures for indoor applications to meet the requirement for corrosion resistance using a standardised coating process, which, once again, ensures a consistent finish to every item produced. Once initial manufacturing is complete, enclosures are cleaned and degreased to ensure that the coatings to be applied will satisfactorily adhere to the product. Immediately after degreasing, the first corrosion protection coating is applied using a nanoceramic pre-treatment. For the second coating, the enclosures are fully submerged in a dip tank and subjected to electrophoretic dipcoat
priming. Corrosion protection is completed with powder coating, which also provides the structure for the enclosures’ outer skin. If, once the enclosure has been installed and the system is in operation, the outermost coating is damaged, there are still two further layers in place to prevent rusting.
For electrical switchgear enclosures, corrosion protection is required by IEC 62208 and IEC 61439. The required corrosion test is conducted in accordance with IEC 60068-2. Depending on the testing standard, a distinction is made between indoor and outdoor installation. To verify corrosion resistance, the corrosion process (which actually takes place over several years) is simulated in just a few days using a salt spray test.
As well as protecting the installed equipment, it’s also the function of an enclosure to protect the people who operate it or work in close proximity to it. The standard IEC 61439, which is applicable to switchgear systems, includes several specifications for the mechanical properties of enclosures for this very reason.
Electrical faults can place high demands on enclosures in the form of increased internal pressure or the magnetic effect of a high short circuit current. An increase in internal pressure can, for instance, be triggered by short circuit shutdown by large circuit-breakers that cause arcing when switched off. Furthermore, the magnetic field that forms around a copper bar particularly at high short circuit currents has an effect not just on the neighbouring copper bar but also on parts of the enclosure, including the mounting plate.
It must be ensured that the enclosure doors do not open during short circuit shutdown and that the busbar system remains secured even in the event of a short circuit. If an enclosure door is blown from its fixings and internal parts ejected, there is a high risk of injury to people in the vicinity of the enclosure.
This is why it is important for an enclosure to maintain its original mechanical strength even after several years and not weaken due to rust or any other factors. Standardised production and coating processes are crucial to ensuring this long-term mechanical strength.
Finally, modular enclosure systems that allow additional panels to be bayed to existing suites in a variety of configurations or cooling solutions to be quickly and easily installed can help to deliver a future-proof system, ensuring that the ideal operating conditions may be provided for existing, upgraded or additional equipment regardless of the external environment.
These are just some reasons why you should take the time to consider the specification of the enclosures being used to protect your equipment.
With regard to sorters, durable, reliable and flexible enclosures may be used to protect equipment and people alike. They play an important but often overlooked role in providing an efficient, low maintenance baggage handling system that operates just as it did on the day it was installed, for years to come.