Optimisation of baggage infrastructure at Copenhagen Airport
- Like
- Digg
- Del
- Tumblr
- VKontakte
- Buffer
- Love This
- Odnoklassniki
- Meneame
- Blogger
- Amazon
- Yahoo Mail
- Gmail
- AOL
- Newsvine
- HackerNews
- Evernote
- MySpace
- Mail.ru
- Viadeo
- Line
- Comments
- Yummly
- SMS
- Viber
- Telegram
- Subscribe
- Skype
- Facebook Messenger
- Kakao
- LiveJournal
- Yammer
- Edgar
- Fintel
- Mix
- Instapaper
- Copy Link
Posted: 3 October 2023 | International Airport Review | No comments yet
In International Airport Review’s Issue 2 2023, Samuel í Hjøllum Rude of Copenhagen Airport discussed how optimisation has increased the utilisation of the baggage infrastructure at the airport.
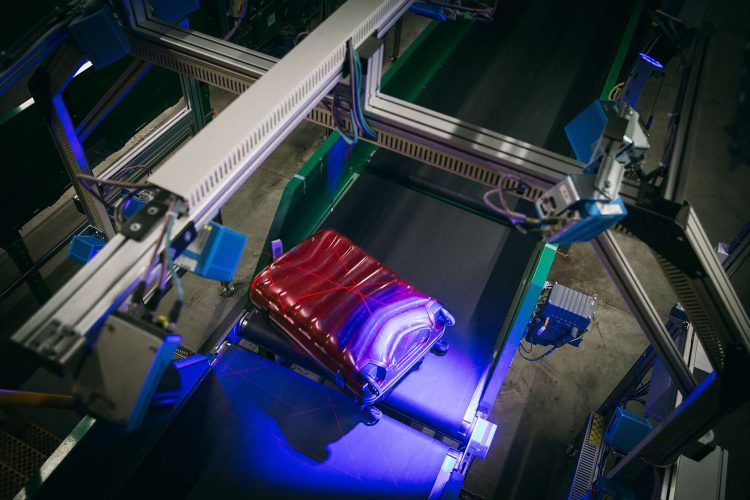
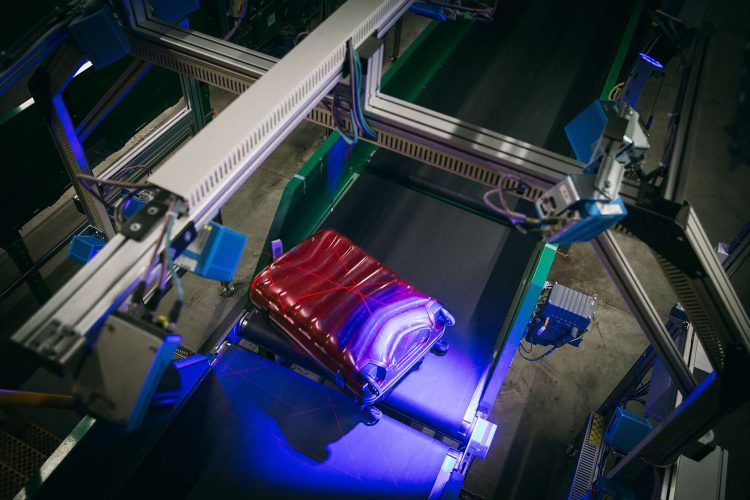
Credit: CPH.
Samuel í Hjøllum Rude, Senior Director at Copenhagen Airport, shares in Issue 2 how optimisation has increased the utilisation of the baggage infrastructure at the airport, allowing for future growth without adding physical infrastructure.
Copenhagen Airport’s (CPH) main sortation facility for outbound baggage turned 25 years old in April. When taken into operation in 1996, CPH had 16.8 million passengers. In 2019, more than 30 million travelled through CPH. In other words, thanks to optimisation, 80% of growth was absorbed using the same main sortation facility. In an earlier article for International Airport Review, we showed how we combine change management and algorithms to optimise. In this article, I will show how we have maximised utilisation of the baggage infrastructure.
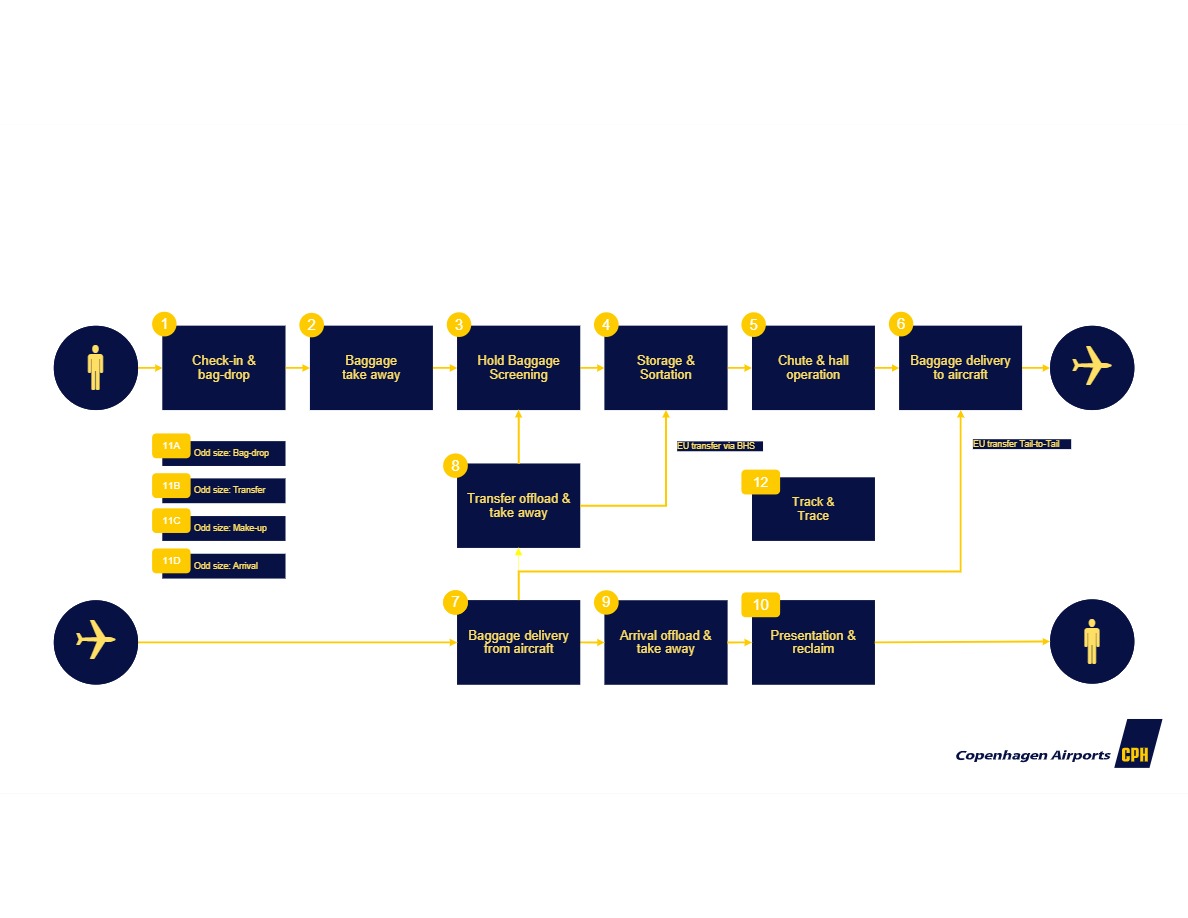
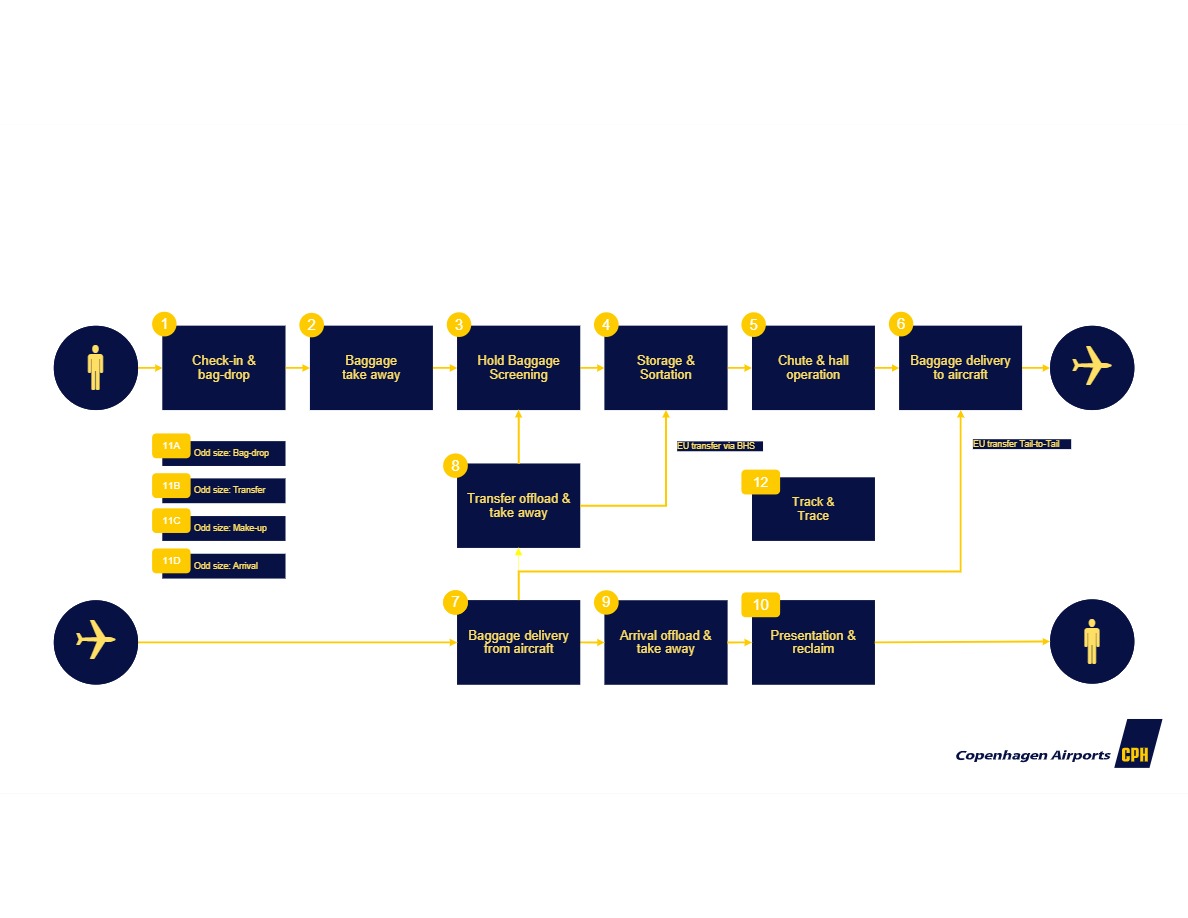
Credit: CPH
Old, but well maintained
The baggage infrastructure in CPH is conveyor based. Our main facility has lane-based Early Baggage Storage (EBS) and two double-stacked tilt tray sortation machines from Crisplant (Beumer). The sorters have been re-controlled, so we are now using a high-level control from Van der Lande. On the arrival side, we have six belts available.
LEAN is at the heart of our operation
The most important part of our optimisation journey is not technical solutions, but the introduction of our morning LEAN board meetings. Here, representatives from the baggage department gather to evaluate the daily KPIs. An essential purpose is also to share information and coordinate maintenance and projects to be executed in a structured manner. The setup is simple and used in many other industries. However, I have yet to see it in airports other than CPH.
The idea is that we have five KPIs, all reflecting critical steps crucial to the quality of our delivery. If a KPI is below the target (red), we have supporting numbers leading us to the root cause, which is then addressed by an action. This approach helps us to build a data-driven culture where we base our solutions on facts rather than gut feeling. It also helps us build operational standards and share knowledge across the team to optimise effectiveness and quality incrementally. This is useful for control room operators and management in our department. It is not only the culture which has become more data-based, but also our approach to allocating resources.
Allocation of arrival belts
When a plane arrives at an airport, the passenger must know where to pick up their luggage. Therefore, airports allocate arrival belts when the aircraft is at the stand. Ideally, from a capacity utilisation perspective, the arrival belt had been assigned when the baggage was ready to be off‑loaded. However, many airports use fixed rules when allocating arrival belts, i.e. the flights are at the same belt day after day. At Copenhagen Airport, an algorithm is doing the job. Based on machine learning, the algorithm predicts when the first- and the last bag is off-loaded at the belt. Using this prediction, the arrival belt is then assigned by an advanced algorithm in real time. We aim to minimise instances with overlaps, i.e. more flights on the same belt simultaneously. A user interface shows the result to the control‑room operator in a Gannt chart. It allows us to act and implement any special needs in the allocation. As a result, the capacity is used most effectively, and the passenger experience is improved.
This approach helps us to build a data‑driven culture where we base our solutions on facts rather than gut feeling.
In addition, a nice feature we have developed with our supplier is a ‘what-if scenario tool’. This tool allows us to ‘play’ with future scenarios. For example, we can see what impact changes in flight schedules or infrastructure have on our capacity and service level. The scenario tool has been valuable in planning our upcoming Terminal 3 Airside project. In this project, we also extend the model to include the allocation of off‑loading transfer stations to minimise minimum connection time.
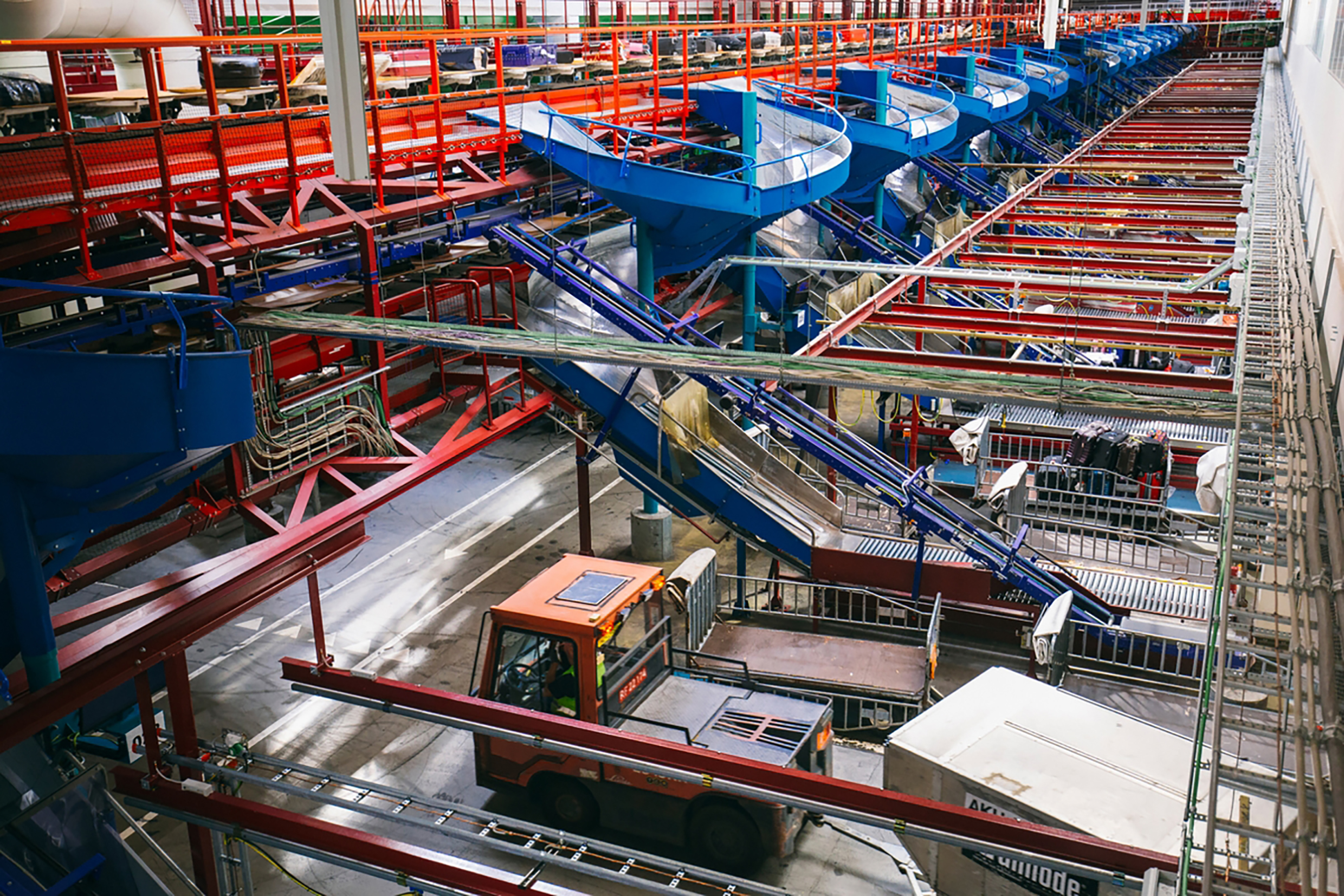
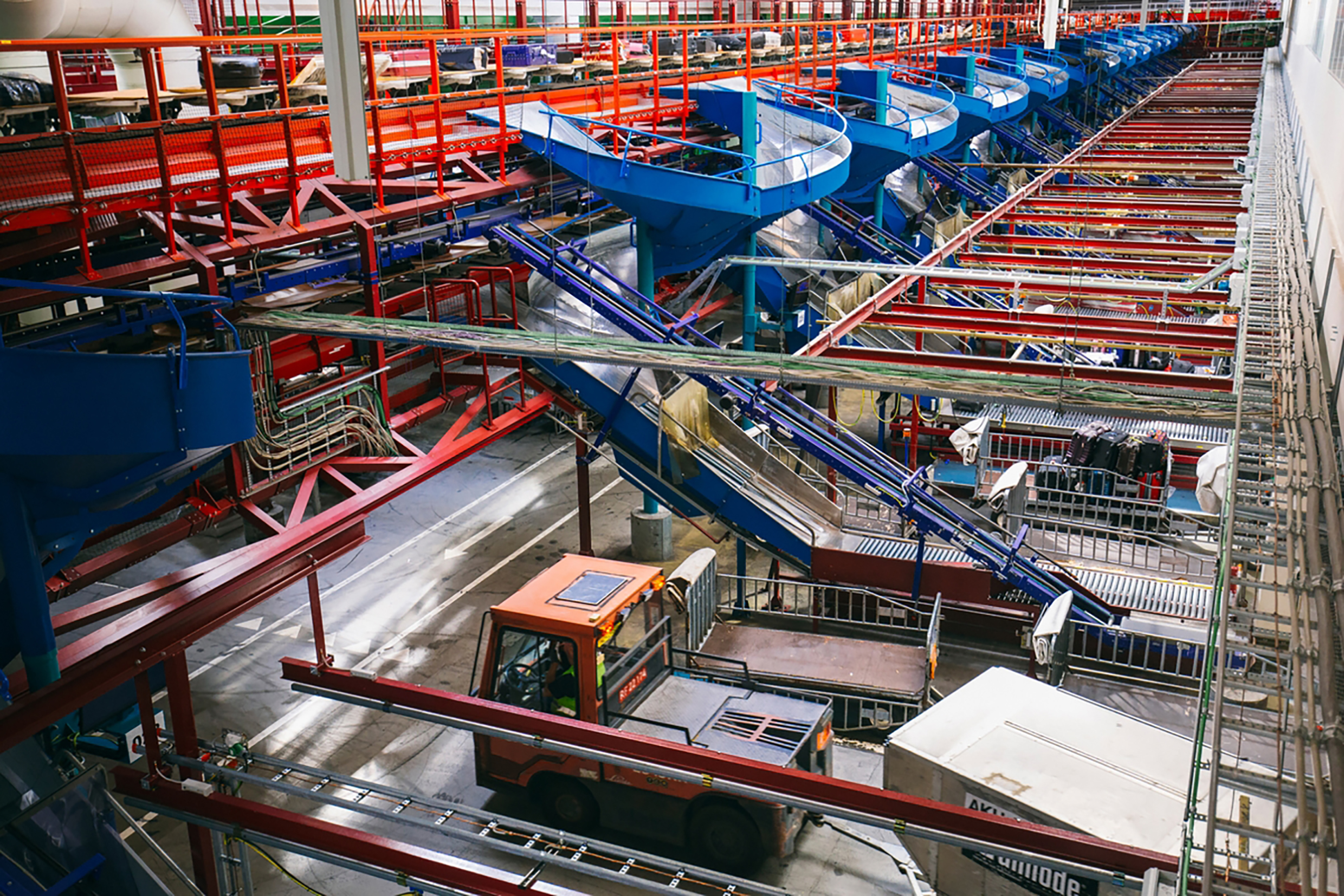
Copenhagen Airports 25 year old main sortation facility. Credit: CPH.
Optimisation from check-in to sortation
Arrival allocation is just one example where the process has been optimised in the existing BHS. In addition, more initiatives have been taken when looking at the baggage process, such as:
- At check-in, an algorithm has been implemented on the PLC level. It maximises the utilisation of the takeaway belt while balancing and minimising the wait time for passengers
we can see what impact changes in flight schedules or infrastructure have on our capacity and service level.”
- The tracking on the conveyor-based system has been improved by adding extra cameras to the Automatic Tag Readers (ATRs) and more ATRs in critical places. This has also improved the read rate, which reduces the volumes for manual encoding
- We have implemented Optical Caracter Recognition (OCR) and remote video coding on manual encoding
- When allocating make-up positions, we use an algorithm for tactical planning. Using this, we forecast the expected baggage volumes on future flights; this determines the number of make-up positions and the opening time of the chutes, which the algorithm distributes in the baggage sortation facility. This maximises how we utilise our main sortation facility.
Learnings from our work with optimisation
As I mentioned earlier, the main sortation facility has now turned 25 years old. I have given some selected optimisation examples from Copenhagen Airport, which have allowed us many years of growth without adding infrastructure.
Some of the main learnings we have made along the way, are how important it is to build a culture pushing optimisation forward. Having a close and honest dialogue with the ground handlers at the airport has also been paramount to our success. Lastly, we have benefitted from using ideas outside our own industry.
Terminal 3 Airside Project – the upcoming expansion of CPH
Everything is not optimisation, however. During COVID-19, we added a small sortation facility; we expect to have a departure capacity of 35‑40 million passengers.
On arrival, we are executing one of the most significant projects in CPH’s history. It will add approximately 2.5km of conveyor belts to our existing system. Our reclaim hall has expanded significantly, and we will add five more reclaim carousels and a new solution for transferring baggage – building CPH for the next generation.
Samuel í Hjøllum Rude is Senior Director at Copenhagen Airports responsible for baggage operations, maintenance, and automatisation. Before joining Copenhagen Airport, Samuel worked with operations in the parcel delivery industry for companies such as DPD and PostNord. Samuel holds a Business Administration diploma and an Executive MBA from Copenhagen Business School.
Issue
Related topics
Airside operations, Baggage handling, Operational efficiency, Terminal operations