Winter services in the face of coronavirus at Frankfurt Airport
- Like
- Digg
- Del
- Tumblr
- VKontakte
- Buffer
- Love This
- Odnoklassniki
- Meneame
- Blogger
- Amazon
- Yahoo Mail
- Gmail
- AOL
- Newsvine
- HackerNews
- Evernote
- MySpace
- Mail.ru
- Viadeo
- Line
- Comments
- Yummly
- SMS
- Viber
- Telegram
- Subscribe
- Skype
- Facebook Messenger
- Kakao
- LiveJournal
- Yammer
- Edgar
- Fintel
- Mix
- Instapaper
- Copy Link
Posted: 25 November 2020 | Daniel Lütscher - Fraport AG | No comments yet
Daniel Lütscher, Head of Fraport AG’s Infrastructure – Airport Facilities and Area Services Department, details how Frankfurt Airport has adapted its winter training due to new challenges.
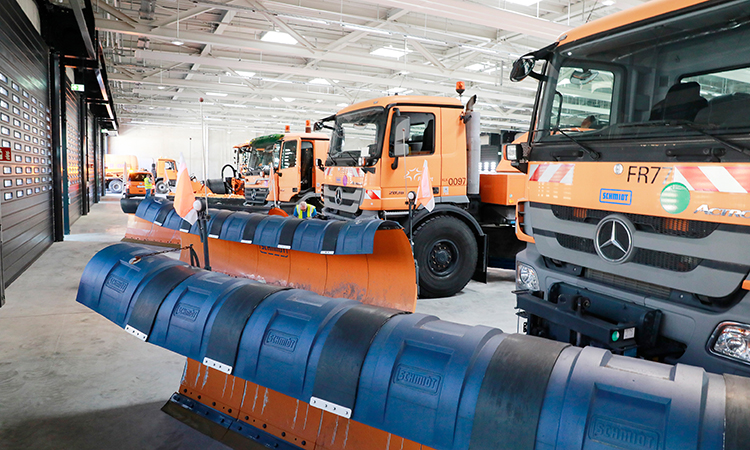
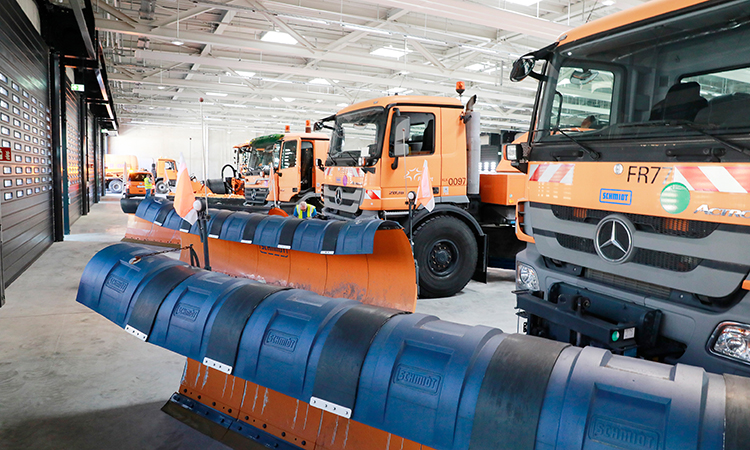
While we are still in the middle of summer, Frankfurt Airport’s (FRA) winter services have already begun to prepare for the new season: Training courses for the upcoming winter start as early as July. With an airport like Frankfurt – one of the biggest in Europe – it may be hard to believe, but the core team for winter services consists of only six permanent employees. The team’s current task is to make the necessary preparations for the next winter, such as ordering new gritting agent, maintaining vehicles and – most importantly – training the new seasonal temporary workers. Every year, the winter services call in approximately 900 seasonal employees, who must be trained to operate snow blowers, gritting vehicles and other equipment on FRA’s airfield.
The effects of COVID-19 on winter operations
This year, however, everything is different and more complex compared to previous years. The coronavirus pandemic has hit the aviation industry hard, including FRA. Passenger traffic declined by approximately 90 per cent at FRA during June, while 18,000 employees were placed on short-time working. Runways and taxiways remain emptier than before – and, most probably, still will be in winter. This poses a challenge to the winter services and the planning for the upcoming season. For example, training courses will have to be adapted to the required hygiene measures, before receiving a high number of participants.
This year, only 600 temporary workers will be trained instead of 900. While usually seven participants are assigned to one trainer, this season the number will be reduced to four. In the training rooms, the distance between seats has been increased to 1.5m. Steering wheels are regularly disinfected and when two people operate the same vehicle, they are required to wear a face mask. It’s not the most comfortable way of training, but it’s necessary to stay safe and healthy.
But where will the 600 new temporary workers for the winter services be recruited from? The answer is simple: From Fraport’s administrative departments. Anyone wanting to temporarily swap an office chair for the driver’s cab of a snow plough is given the opportunity, thanks to a special initiative launched by Fraport. To ensure that enough personnel are available, we are recruiting hundreds of colleagues who otherwise work in administrative positions at the airport.
This year, the administrative employees are even more important than before – due to the effects of the coronavirus pandemic. In normal times, Fraport’s winter services also rely on external seasonal staff. For example, farmers from the region, who assist the winter services every year, are already well versed in the procedures and in handling the heavy equipment. As a result of the pandemic, they can’t be on board this year. This means that almost all temporary workers hired for this season are untrained recruits, who have to be trained as fast as possible and under exceptional circumstances. Fortunately, the winter services are used to coping with challenges. That’s what our job is all about – extreme situations.
Benefits from COVID-19
On the other hand, in this overall very difficult economic situation, the coronavirus pandemic has had some beneficial effects on winter services – particularly in regard to training conditions.
Due to the reduced air traffic, FRA’s Runway 18 West is currently closed and therefore available for training. Previously, new recruits could only be trained outside the runways. Now, they can practice directly on the runway, which is much more efficient.
Equipment and resources required at FRA
FRA’s winter services are responsible for keeping the airport’s entire operational area – covering 9,027,000m2 – free of ice and snow. This can only be done with good planning, efficient training and a sufficient supply of resources. The fleet of equipment is comprised of 384 vehicles, including 24 spreading vehicles, 78 de-icing trucks and 110 other trucks. When operating over a full period of 14 days, the winter services require 750 tonnes of salt and 160 tonnes of sand. An average of 1,700,000 litres of aircraft de-icing agent is required for only five days of operation.
Snow, in particular, is no longer one of the main issues the winter services have to deal with”
This high quantity of equipment and resources is necessary, despite the fact that winters are becoming milder year by year. Snow, in particular, is no longer one of the main issues the winter services have to deal with. During the winter of 2019/20, FRA saw only one day of snow for the entire season. Still, everything needs to be ready if a sudden winterstorm hits the ground. Therefore, precautionary gritting is carried out regularly. Apart from removing snow and ice, the staff also perform other essential tasks, such as cleaning airport surfaces or irrigating green areas. FRA’s winter services thus contribute to ensuring safe and smooth operations all year round – not only in winter.
In 2019, the winter services moved into a new building, where everything is under one roof. Before, the control centre and various vehicles were located in different buildings across the airport grounds. Now, operations have been centralised, with all 384 vehicles available in one location; resulting in greater efficiency. The new building also features state-of-the-art training rooms equipped with the latest technology. We are always working towards becoming faster and the new building makes that easier.
Greater efficiency and faster training were also achieved thanks to a recent upgrade to the equipment. Unlike before, many vehicles – especially runway sweepers and spreading vehicles – are now operated in identical ways. The advantage is new recruits have to be trained only on one operating system and are then able to operate all vehicles of the same type. Vehicles have also been retrofitted with additional hardware, such as joysticks and extra buttons, making it easier to operate them. The environment also benefits from this upgrade: Equipped with special spray nozzles, the new vehicles can apply the de-icing agent more precisely than older vehicles with spreading discs. This saves de-icing agent – and money.
Thanks to on-going optimisation measures like these, FRA’s winter services are moving towards the future with ever-increased efficiency”
Thanks to on-going optimisation measures like these, FRA’s winter services are moving towards the future with ever-increased efficiency. The future appears to be exciting and challenging amid the coronavirus pandemic – with stricter hygiene measures in place for training courses, but also more efficient teaching methods available. Moreover, vehicles and equipment are constantly being further developed. Just as in previous years, this season will again give many non-operational employees an opportunity at Frankfurt Airport to swap the office for a snow plough
Daniel Lütscher has in-depth knowledge of Frankfurt Airport (FRA) and its infrastructural and operational processes. He started his career at FRA 27 years ago as a trainee for office management. Winter 2019/20 marked his fourth season as Head of Fraport AG’s Infrastructure – Airport Facilities and Area Services Department. In this role, he is responsible for FRA’s winter services, as well as for the management of the airfield lighting system, the people mover system and the passenger boarding bridges.
Issue
Related topics
Airside operations, COVID-19, Economy, Machinery, Passenger volumes, Recruitment and training, Winter operations, Workforce