Planning for winter at Glasgow Airport
- Like
- Digg
- Del
- Tumblr
- VKontakte
- Buffer
- Love This
- Odnoklassniki
- Meneame
- Blogger
- Amazon
- Yahoo Mail
- Gmail
- AOL
- Newsvine
- HackerNews
- Evernote
- MySpace
- Mail.ru
- Viadeo
- Line
- Comments
- Yummly
- SMS
- Viber
- Telegram
- Subscribe
- Skype
- Facebook Messenger
- Kakao
- LiveJournal
- Yammer
- Edgar
- Fintel
- Mix
- Instapaper
- Copy Link
Posted: 21 July 2017 | Louise Hurst | No comments yet
In an interview for International Airport Review, Louise Hurst, Glasgow Airport’s Airside Operations Manager, provides an overview of the airport’s winter operation activities and explores the benefits her team can acquire from advances in technology.
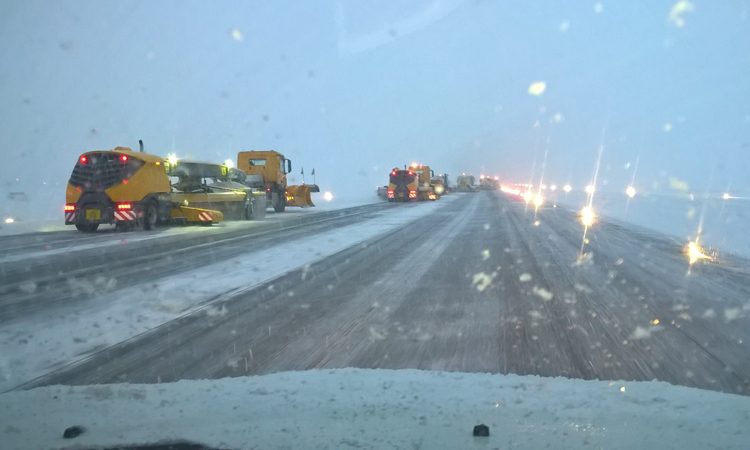
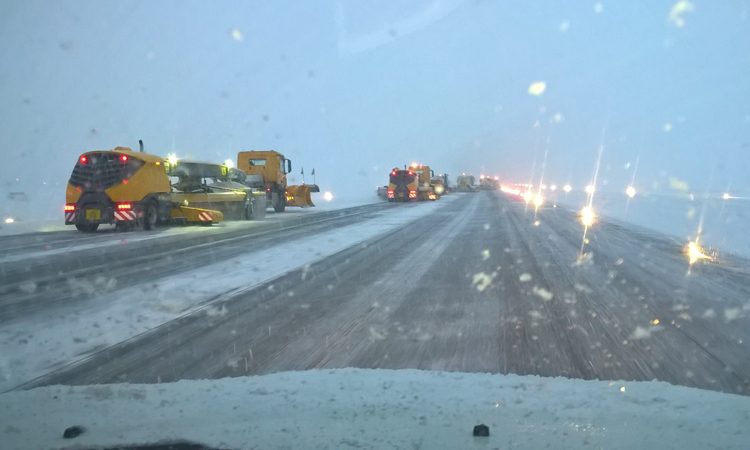
How does Glasgow Airport deal with the winter season?
We do so in several different ways. The results of extensive planning are put in place, which, given we live in Scotland, can be year-round for the operations team.
There are a couple of obvious months of the year where winter operations are less intensive, but we still deal with a number of different weather-related circumstances. This could be cold weather, severe wind, heavy rain, or ice right up to snow in its different variations. Lots of planning, people, equipment and training goes into making sure we’re ready and prepared. We also work with a lot of suppliers and contractors to ensure that everything is set up to go when bad weather hits.
Airside Operations and the Airside Service Unit (ASU) form part of our runway and airside inspection teams. They work on a five-month stand-by roster, which runs parallel to their own shift plans. We also operate a volunteer programme made up of staff drawn from across Glasgow Airport Ltd’s own workforce, which includes security staff and members of the duty, safety and ambassador teams. Last year we had 96 volunteers from every area of airport life – even staff from the taxi desk – get involved in supporting our winter operations programme.
What lessons have been learnt from previous years and how are these applied to the winter preparation process?
The worst winter scenario I’ve been involved in was in 2010, when the entire UK was blanketed with snow. I think the biggest challenge we face generally – certainly in the UK – is that we don’t see enough snow to gain the necessary expertise to operate, clear or manage it. The biggest difference for the UK, as opposed to Continental Europe or Canada for example, is the type of snow we get. Other countries will have white, powdered snow that compacts and can be worked on fairly easily, whereas we get wet, slushy snow, which compacts into ice and becomes a very different issue. From our perspective, the machinery we operate is important. We currently have five Overaasen RS 400s, which are used to clear the runway and work in tandem with the three SB 90s we also use for taxiways. They are great pieces of kit and, most importantly, work at speed and allow us to clear our runway and taxiways quickly and effectively.
Over the past five years, certainly compared to 2010, we’ve experienced very little snowfall. However, this doesn’t make the winters any easier because we spend the whole season studying weather reports from providers. We also need to make sure we have the right number of people on stand-by and that our equipment and supplies are ready to go; making sure the right amount of de-icer fluid is ready, the tanks are full and the equipment is in working order. It is also important to ensure employees are properly trained in the lead up to winter and that staff are using the equipment consistently to keep competency levels up. It’s about dealing with all winter weather, not just snow. All year-round provisions must be in place to ensure people and equipment are ready to go.
On 16 January 2016, heavy snow was forecast and we activated the teams before it started and everyone was ready and in place. Eight hours of snow was forecast, but it actually fell for longer due to how the weather was moving. We all know weather is unpredictable, no matter how well it is forecast. It progresses and can move around you. We normally receive a fair bit of protection from the hills around the airport, but on that day it came through us and snowed consistently for 14 hours. This was tremendously challenging for the team. We were clearing snow constantly from start to finish, which can be demoralising. A volunteer could be out clearing a 100m walkway with a shovel and de-icing granules and by the time they reach one end, the other end is white again. It’s the same with clearing the runway too – it can be a constant, challenging process.
In these circumstances we tend to be as proactive as possible, constantly considering such aspects as: Which aircraft is operating? Which is next to go out? When is the next arrival so we can ensure the correct stand is prepared to make it safe for passengers to embark and disembark the aircraft?
The time at which winter operations teams are activated is also really important: the earlier the better, of course. Generally, the first call out is fine as the snow might not even have started at this point, or it may only be very light. The roads would normally be gritted and so on. We are fortunate that Glasgow Airport is based near a good road network. Many of our staff also live relatively near, which definitely helps when assembling the team.
Prolonged, heavy snowfall would represent a bigger challenge, particularly if it moved in quickly, as people on the next shift could potentially be snowed in. If this were the case, we have a contingency plan to dispatch a minibus to meet them at pre-arranged points. We also have access to a 24-hour weather forecaster through the full winter season and they provide us with live RADAR feeds and satellite imaging for the airport. We essentially have a round-the-clock hotline to our forecaster, so we communicate constantly to monitor weather patterns.
How do you envisage the increasing role of technology will alter the way airside operations are carried out?
I think we can only benefit from advances in technology. Tools such as GPS and live RADAR feeds are vital when it comes to clearing our airfield, particularly when using real-time data. It also allows the monitoring of weather patterns and enables tweaks to be made to improve operational effectiveness. Technology provides far greater detail, which is hugely beneficial in terms of planning. There is far greater confidence that resources are deployed in the right place; that correct materials are being used; and that resources are being utilised in the best way at any given time.
Social media is also of great benefit. For example, our winter operations volunteers use a closed Facebook page and we have found this to be a simple, but really useful, resource in terms of communication and intelligence sharing.
We are currently looking at a new de-icing machine that will give us real-time GPS data, enabling us to plot and utilise it more efficiently. It records and relays real-time accurate measurements to show, for example, coverage of a specific area, allowing us to drill down on effectiveness.
There is an increased focus on environmental responsibility across the entire airport sector – how has this affected winter operations and the equipment/products used?
There is a legal requirement for the airport to ensure that any products used in our operations are approved by the Scottish Environment Protection Agency (SEPA). In addition to being a legal requirement, it is also a moral one. We are based in a geographically challenging area with the White Cart and Black Cart rivers, which both feed the River Clyde, flanking the airport campus. As a consequence, any products or supplies we use – or would like to use – must rightly be tested and approved by SEPA, with whom we work closely.
What changes do you expect to see in the industry going forward?
Equipment, products and technology are constantly evolving and this will ultimately improve operational performance. Airports are getting bigger and busier, which means more growth and even greater demand. In order to meet this demand, more emphasis will be placed on efficiency in an operational sense. This will obviously mean greater collaboration between airlines, our operational teams and ground-handlers.
Glasgow Airport prides itself on its one-campus culture and it works very well. As the airport grows, the way in which we work together as a campus will continue to be a key driver in delivering operational effectiveness and success.
Biography
Louise Hurst became Glasgow Airport Airside Operations Manager in May 2014, having previously worked with Menzies Aviation. She was also Station Manager at Glasgow for two years before joining Glasgow Airport Ltd. Louise’s airport career started in 1998 with BMI where she worked as a Customer Service agent at check-in. She has held various roles at other UK airports including Load Control, Supervisor, Service Delivery Manager and she also completed a year-long management development programme with Menzies in 2011, which gave Louise a rounded understanding of all roles within a ground handling business.