Does small-scale fire testing reliably increase safety?
- Like
- Digg
- Del
- Tumblr
- VKontakte
- Buffer
- Love This
- Odnoklassniki
- Meneame
- Blogger
- Amazon
- Yahoo Mail
- Gmail
- AOL
- Newsvine
- HackerNews
- Evernote
- MySpace
- Mail.ru
- Viadeo
- Line
- Comments
- Yummly
- SMS
- Viber
- Telegram
- Subscribe
- Skype
- Facebook Messenger
- Kakao
- LiveJournal
- Yammer
- Edgar
- Fintel
- Mix
- Instapaper
- Copy Link
Posted: 13 December 2019 | Mike Willson (Fire Protection Consultant) | 2 comments
Mike Willson, fire-fighting foam specialist, investigates whether passenger and staff safety is at a greater risk in Australia due to incorrect use of fire‑fighting foams and uncompromising regulations.
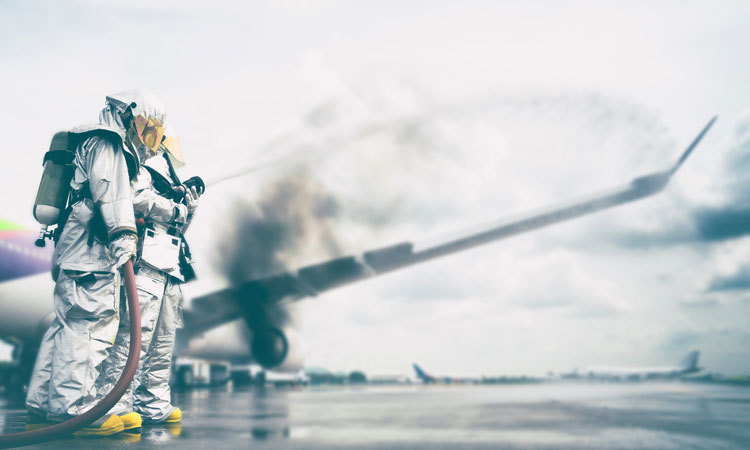
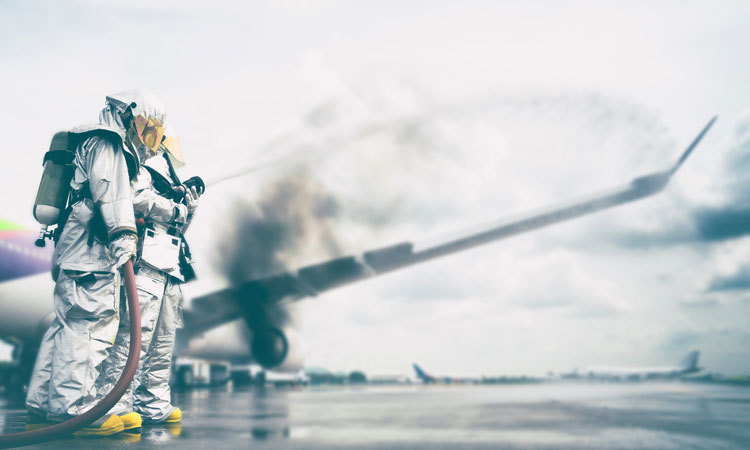
A recent Australian Senate inquiry was held into the provision of fighting fire and emergency responses at Australian airports. The August 2019 report made some interesting recommendations, which has relevance to airports worldwide.
These Senate recommendations include an audit of all ARFF vehicles and equipment to ensure they meet ICAO requirements, with a review of adherences to ICAO and recommended best practices for the future provision of ARFF services in Australia.
Australia may not be following best practice
Currently, the vehicles provided are on the limit of volume acceptability for water and foam, with staffing often shared between ARFF services and other emergencies around the airport. These typically include building fire alarm activations and terminal medical emergencies; occurrences that are not generally considered aircraft emergencies. Undesirable category reductions can result when firefighters are engaged in such tasks, causing concern and questioning.
It also requires the Civil Aviation Safety Authority (CASA) to conduct a Task Resources Analysis (TRA) to determine necessary ARFF staffing levels. This must involve appropriate consultation with ARFF staff at all stages so their views and past experiences can be incorporated. Concerns were raised over proposals to increase the threshold to 500,000 (from 350,000) passenger movements to justify an ARFF service at Australian airports. In comparison, in Canada, 180,000 passenger movements triggers an ARFF service provision.
Some airports, with high aircraft movements but lower passenger numbers, potentially require ARFF services where none currently exist. The report recognised that “a lack of serious incidents in Australia may have led to a sense of complacency, where decisions may have been taken based on the likelihood of ‘nothing happening’ rather than ‘in all probability one day it will’”. ICAO suggests a risk-based approach, in which probable and credible worst-case scenarios should be followed. The report accepted that a lack of adherence to relevant international standards in Australia was placing the safety of firefighters, and of others, at risk.
ICAO Level B test conditions
For the first time, this report recognised ICAO’s Level B and C fire tests do not adequately reflect Australian climate conditions for most of the year. The committee recommended Australia’s government conduct a review of the country’s adherence to ICAO’s standards and recommended best practices for the provision of ARFF services. Where the review identifies non-compliance with international standards, the rationale for this should be fully explained, or corrected.
This report highlighted reliance on a single small ICAO fire test approval in freshwater, conducted as close to 15°C as possible, and since its changes in 2014, also now permits fire extinction within 120 seconds. This determines the acceptability of fire-fighting foams to protect a wide range of aircraft, potentially carrying around 500 passengers and 310,000 litres of fuel in a single Airbus A380. Concerns exist that the small fire test may no longer be an adequate re-assurance of reliable capability, under the wide range of prevailing conditions at aircraft incidents and accidents worldwide. Actual application rates provide a safety margin above these test rates, to compensate for numerous variables including temperature, delayed response, wind, rain, hot metals, obstructions, faulty equipment, foam blanket interruption and training shortfalls, but has this margin been significantly eroded by ICAO’s 2014 changes?
The relevance of a small single fire test to verify passenger, crew and firefighter safety in major incidents seems to have become blurred in recent years, and may not represent the larger scale, worst-case conditions in air accidents potentially affecting passengers each year in Australia. This is particularly true considering all U.S. airports are protected by foams undergoing a tougher, more stringent and rigorous MilF Specification fire test, correlated by large-scale 580m2 fire test data using Jet A fuel confirmed by Scheffey’s 1994 research. MilSpec qualification requires passing seven different fire tests, including fresh and seawater, full-strength and half-strength tests, inter-agent compatibility, smaller and larger fire areas at challenging application rates, elevated pre-conditioning tests, dry chemical compatibility tests, corrosion and environmental requirements (only one of which is included in ICAO, but many are highly relevant to Civil Aviation), and which Fluorine Free Foams seem unable to pass. Yet most airports are accepting the single test ICAO Level B or C approved foams for use under widely varying conditions and for all aircraft sizes and specifications.
Why is NFPA 403 relaxing response times?
Other aviation standards like NFPA 403:2018 seem to be relaxing rather than strengthening response times. This standard confusingly recognises ICAO’s single Level C fire test in freshwater only to be “equivalent to the U.S. Mil Spec PRF24385F (SH)”. There is no explanation of how – please read my previous International Airport Review article, “Focusing on the best fire protection” in Issue 6 2018 for a detailed comparison.
Similarly, application rates of ICAO at 1.56L/min/m2, compared to MilSpec’s 1.64L/min/m2, may seem superficially sufficient, but are they? AFFF at ICAO Level C may work as effectively on MilSpec and vice versa, but it seems increasingly unlikely to be the case with F3s where greater fuel differences and unpredictability are becoming evident. Increased rigor of MilSpec requiring all qualified foams to pass seven tough fire tests places far more pressure on foams to perform. Does this not better replicate potentially more onerous conditions that will likely be faced? This MilSpec protocol still eludes any F3 agent from passing not just the fire performance aspects, but environmental tests and often dry chemical compatibility. Surely “dumbing down” fire protection standards – as seems the case with ICAO and now NFPA 403 – could increase the likelihood of a major disaster?
Fluorinated foams have saved many lives
We should not forget why the unique fuel shedding benefits of AFFFs were developed, following the USS Forrestal disaster in 1967. Many people died and were seriously injured because a non-fluorinated foam was seemingly too slow to act and control the developing fire.
Following this tragedy, AFFFs were fast tracked for development, using rigorous small-and large-scale fire testing to secure adequate safety margins and avoid such a tragedy ever happening again. One has not been repeated for over 50 years: Are we getting complacent and less willing to use the best foam agents available? This is particularly true in regard to aircraft with enormous fuel loads, or at airports with aircraft landing and taking off with less than 60 second intervals. A “rule of thumb” suggests a survivable atmosphere inside an aircraft fuselage can last for approximately three minutes. Extending the response time, where slower acting non-fluorinated foams are being used, may be a recipe for disaster, particularly under more severe climatic conditions.
Is passenger safety being compromised in Australia?
The Senate Report has recognised these concerns, highlighting how “the committee was alarmed by the evidence regarding fire-fighting foams, and the fact that the foams in use at Australian airports may not have been tested to Australian standards. The committee notes that ICAO’s international framework for testing foams may not be suitable for the conditions at local aerodromes”.
Foams under ICAO Level B or C are normally tested as close to 15°C as possible, with no requirements for repeats. But this hardly reflects the temperatures experienced at most of Australia’s main airports. The Bureau of Meteorology weather data confirms maximum ambient temperatures at 13 Australian airports in 2018 – for at least one month – were 40°C or above. Two airports experienced days of 40°C during seven months within the year, and another two airports experienced five months of temperatures over 40°C.
Many places across the globe exceed the 15°C test temperature, at least in summer, which could be placing the travelling public under unexpected and unnecessarily increased danger.
The report recommends “CASA implement a testing programme for the fire-fighting foams in use at Australian airports, in accordance with ICAO. The testing should take place under conditions unique to Australia (such as higher ambient temperatures), to establish whether the foams operate effectively enough to extinguish aviation fires” in the interest of the travelling public’s safety.
The report drew attention to a “submission that noted that there were considerable benefits to using C6 foams: The faster the fire is controlled and extinguished, the smaller the incident. Any realistic consideration of environmental impacts must focus on the whole incident from fire and environmental performances, not just fire-fighting foam properties in isolation.”
The report also noted: “However, the UFUAB said there was significant evidence for concern as to the real operational effectiveness of the primary [F3] fire-fighting agent in use for ARFFS in Australia. The UFUAB therefore questioned whether the ARFFS was provided with enough quantities of this agent, particularly at Category 9 airports.” This is interesting, as Australia kept water levels to 24,000 litres for the Category 9 airports, despite ICAO raising its recommendations to 27,859 litres in 2015.
The report also recognised: “The FPAA explained that F3 foams have ‘significantly different physical and fire-fighting properties’ to other foams, which could impact on safety outcomes. The FPAA argued that any fire-fighting foam being considered for use on Australian aerodromes should be subjected to ICAO testing, but at ‘much higher minimum temperatures’ to better reflect the Australian climate.”
Gasoline is problematic for F3s
Confidence in small fire tests has been further shaken by recent U.S. Naval Research Laboratory testing. This demonstrated that F3s behave very differently on gasoline in comparison to heptane, with gasoline being the more challenging fuel. All four commercial F3s tested highlighted this problem. Fluorinated foams generally have very similar fire control and extinction results on gasoline as they do on heptane, and therefore heptane is a widely-used test fuel in several popular approval tests including UL162, EN1568-3, FM5130, Lastfire etc. Hence, everyone has assumed the AFFF read across to gasoline also applies to F3s – which is incorrect.
This raises serious questions about reliance on “F3 approvals” using heptane test fuel in the future, following the demonstrated inadequacy on gasoline hazards. Standards must adopt a gasoline alternative test fuel – like Heptane plus 25 per cent TriMethylBenzene, which behaves like gasoline – which F3s must pass to be considered suitable for future use on gasoline type fuels.
NRL also found the best commercial F3 agent tested required around three times more foam to achieve a 50-second extinction time on gasoline in comparison to the control C6AFFF. This factor of three is widely supported by other research. The worst of the four commercial F3s tested required eight times more foam to achieve the same 50-second extinction as the C6AFFF. These results show a very significant, concerning and unexpected variability in F3’s effectiveness on gasoline.
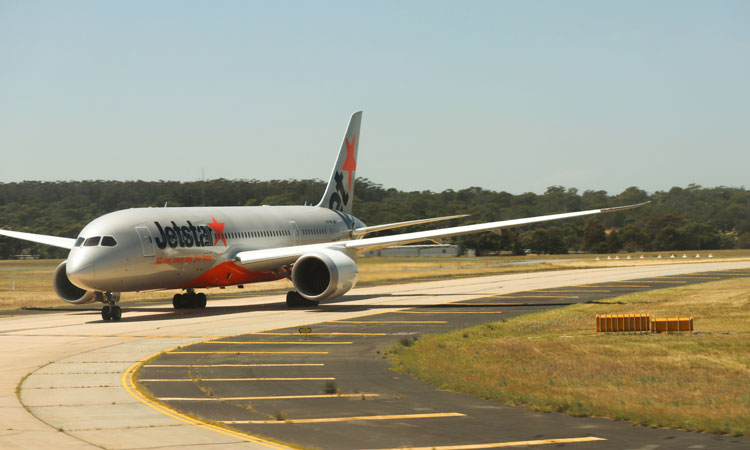
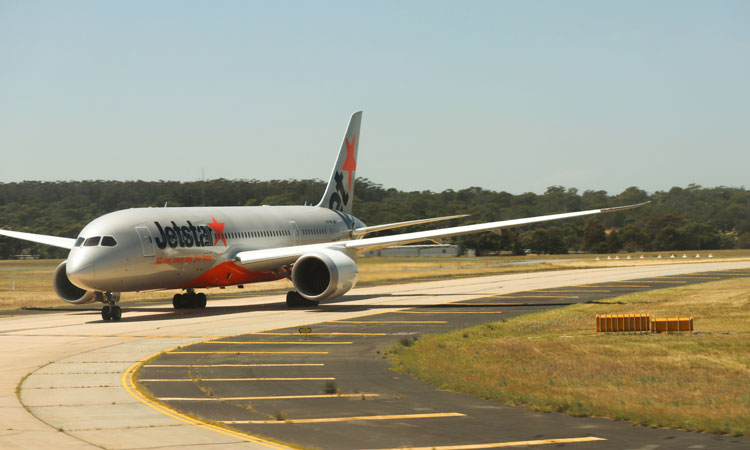
Australian weather makes the landscape susceptible to fires starting
No F3 design guidance for fixed foam
It was also found that there is currently no reliable design system guidance for F3s in fixed foam systems. Comparative UL testing has shown – despite higher application rates generally necessary for F3s – lower expansion ratios (often delivered by equipment on site) can still result in failure, because they generally work more effectively at optimum expansions on specific test fuels. Therefore, it is important to test the specific delivery equipment expansion ratio using F3 or C6 before purchasing, to provide assurance that safety levels will not be compromised.
Lacking evidence of real-life success
Interestingly, the report also noted that it “could not identify ‘any major aircraft fire successfully and quickly extinguished’ by F3. The submission questioned whether this foam had been adequately tested at a larger scale to address the major hazards of Airbus A380 aircraft, increased passenger numbers and flight frequencies, larger fuel loads, and increasingly volatile climatic conditions experienced across Australia.”
The Fire Protection Association Australia’s Special Hazards Technical Advisory Committee established a specialist foam working group to consider issues raised. It aims to work with CASA to ensure realistic F3 fire testing is carried out, and to better understand whether it performs adequately at elevated temperatures.
There are concerns, particularly since this same foam failed a 2016 ICAO Level B demonstration in Singapore at just 32°C, which was successfully extinguished by C6AFFF. F3 also failed to control the major Boeing 777 engine detachment fire in Dubai in 2016; resulting in a potentially unnecessary fatality, plus subsequent destruction of the aircraft.
The industry may require a foam change
The high temperature tests may confirm F3 suitability, may require a different F3 to demonstrate temperature capability, or may revert to a MilSpec qualified environmentally-friendly, fast-acting high purity C6AFFF, relying on unique fuel-shedding and film-forming benefits. C6 AFFF should be expected to work effectively at over 40°C; providing critical protection for passengers, crew and firefighters in all Australian conditions. The key objective of this Senate testing requirement is to avoid placing any life in increased danger. So, shouldn’t large scale >500m2 fire testing at equally low application rates also be required to correlate these small approval tests in the future?
The good news is this high temperature testing represents a step towards improved safety for everyone. Should it be required for other small-scale tests in future? Foams adequately tested and proven sufficiently reliable and effective to pass this demanding high temperature test could then be considered better suited to addressing ambient conditions at many other airports, particularly if accompanied by large scale correlation tests, as has already been achieved for AFFFs meeting U.S. MilSpec.
Biography
Mike Willson is a fire-fighting foam and foam systems specialist with over 30 years’ experience of developing, testing, comparing and reviewing fire performance and environmental impacts of both fluorinated and fluorine-free foams, plus their delivery devices and integrated fixed systems. He was instrumental in developing improved tank fire, bund protection and LNG recommendations in the EN13565-2: 2009 Foam Systems Standard. He also coordinated several emergency foam responses to major incidents worldwide. As an active member of Fire Protection Association Australia’s Special Hazards Technical Advisory Committee, Willson provides technical advice to a diverse range of stakeholders to better protect Class B flammable liquids with potentially suitable C6 and F3 alternatives.
Issue
Related topics
Aircraft rescue and firefighting (ARFF), Airport crisis management, Airside operations, Regulation and Legislation, Safety
How can I examine the foam and get the certificates of an accredited laboratory at ICAO level B
Thanks for your Q Yaser, apologies for the delayed response but I have been overseas with infrequent internet access.
ICAO Level B is a fire test protocol, certificates for which should be available from the firefighting foam’s manufacturer. If the foam is 5 years old or more, it is probably worth gaining a laboratory assessment of its continued suitability by an accredited testing laboratory. The foam’s manufacturer or local distributor should be able to provide details of a suitable foam testing facility. Best regards,
Mike.