ARFF and recovery: Focusing on the best fire protection
- Like
- Digg
- Del
- Tumblr
- VKontakte
- Buffer
- Love This
- Odnoklassniki
- Meneame
- Blogger
- Amazon
- Yahoo Mail
- Gmail
- AOL
- Newsvine
- HackerNews
- Evernote
- MySpace
- Mail.ru
- Viadeo
- Line
- Comments
- Yummly
- SMS
- Viber
- Telegram
- Subscribe
- Skype
- Facebook Messenger
- Kakao
- LiveJournal
- Yammer
- Edgar
- Fintel
- Mix
- Instapaper
- Copy Link
Posted: 27 December 2018 | Mike Wilson | No comments yet
Fire Protection Consultant, Mike Willson, questions whether we are using our best fire protection at airports and major hazard facilities. And if not, why not?
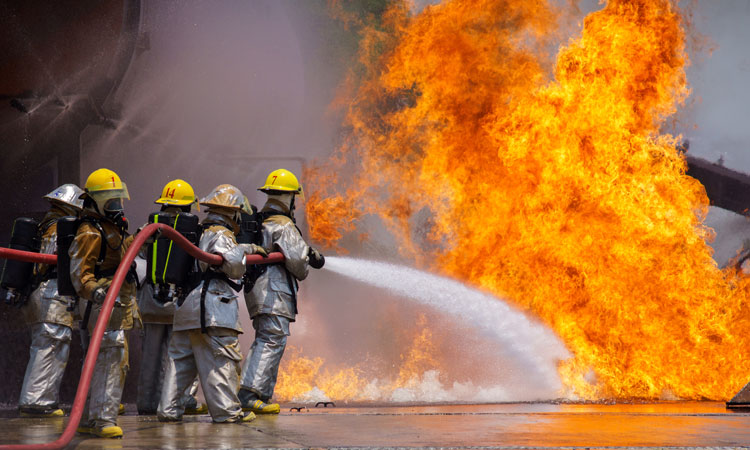
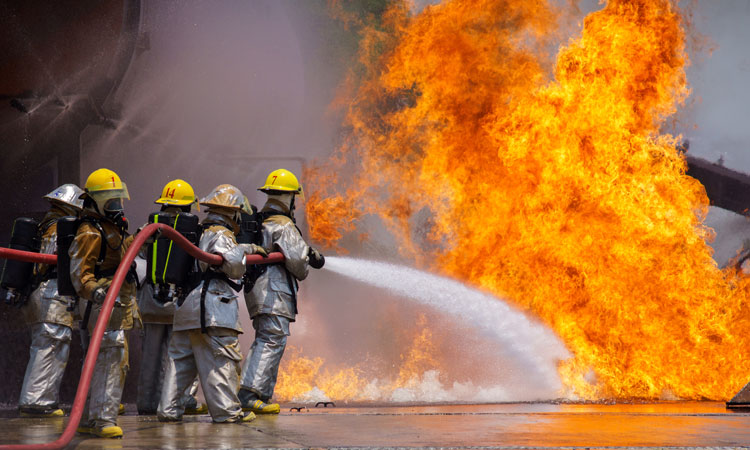
The passing of the Federal Aviation Administration (FAA)’s Re-Authorisation Act, in October 2018, confirmed that FAA-regulated airports “shall not require the use of fluorinated chemicals to meet the performance standards” within three years. 2018’s version of the National Fire Protection Association (NFPA) 403 has also changed, although this means fluorinated foams can still be used. The USA’s Washington State backed off a proposed complete per- and poly-fluoroalkyl substances (PFAS) ban, accepting fluorine free foam (F3) usage for firefighter training from July 2018, plus its amended PFAS restriction legislation passed in March 2018, specifically exempting major hazard facilities – airports, military, oil refineries, petroleum terminals and chemical plants from such restrictions – from July 2020 onwards: a sensible and precautionary approach.
The standard, NFPA 403: 2018, and some industry foam users suggest a “level of equivalency” exists between International Civil Aviation Organisation (ICAO), in its latest Level C fire test and the U.S. Department of Defense Military Specification MIL-PRF-24385F(SH) with Amendment 2:2017 (MilF specification), which negates the necessity for fluorine. This MilF specification is recognised as the world’s toughest fire performance standard for foam agents. Currently no F3 can pass its fire, environmental or supplementary performance criteria. So how can ICAO Level C be considered its equal? Significant differences and similarities need exploring.
What might ‘level of equivalency’ look like?
The key acceptability standard reference point for most major civil airport authorities and operators worldwide (outside USA and China) is ICAO’s current single freshwater Level B fire performance test, at 2.5L/min/m2 on a small circular 4.5m2 tray, conducted according to ICAO’s Airport Services Manual Part 1 Rescue and Firefighting (Doc 9137 – AN/898), fourth edition 2014.
2014 saw a new tougher Level C added, using the same UNI86 nozzle and flow rate (as Level B) but over a larger 7.32m2 fire area, reducing the application rate to a challenging 1.56L/min/m2 (37 per cent reduction from Level B). Not widely used yet, Level C is intended to permit fewer, smaller fire trucks at major airports, helping reduce future aircraft rescue and firefighting (ARFF) costs. A big question remains – can it reliably deliver the fast acting, effective, fire control necessary to protect life safety? Particularly when increasingly diverse and extreme conditions – larger aircraft, more passengers, bigger fuel loads (e.g. A380s) – are being experienced, increasing life safety risks and firefighter challenges? Any equivalency starts to become perplexing when understanding these two quite different fire test standards. 2014 also saw this important global ICAO firefighting standard’s Level B and C fire tests updated, some say diluted; facilitating lower quality AFFFs and F3s to qualify at Level B. The implications of these important changes eroding safety margins, seem to be pulling against notions of ‘equivalency’.
Substantial differences
Pre-2014, ICAO-specified Jet A1 fuel (flashpoint 38°C), widely used by commercial jets but un-ignitable with matches. Acceptance of broader Kerosene (37- 65°C flashpoint) is potentially easier to pass at Levels B and C, especially when relaxing extinction from 60 to 120 seconds.
U.S. MilF specification applies to U.S. Military installations, military fixed and rotary wing aircraft, civil aviation in the USA, plus a very diverse range of vehicles (including aircraft carriers), applications and fuels. Consequently, the most volatile commonly-used fuel was selected– unleaded gasoline (flash point -43°C). MilF specification requires passing seven different fire tests in fresh and seawater. It uses a similar application rate of 1.64L/min/m2 on its larger 4.64m2 tray, also requiring half-strength on the smaller 2.6m2 tray (effectively 1.46L/min/m2 ), plus an over-rich seawater test – guaranteeing safety factors if foam proportioners run lean, or rich. If 20 per cent under-induced would a borderline ICAO Level B or C foam still pass? Particularly when ICAO benefits from accepting less volatile fuel and slower (more than double) extinction. Does this sound like equivalency?
Application rate and foam quality similarities
‘Equivalency’ seems to end with application rates. Many major civil airports, such as Osaka, LaGuardia-NY and Sydney, jut into seas. Might they also require supplemental seawater in major plane crashes? This is an issue ICAO fails to address, potentially relevant when most detergent-based foams struggle with seawater, particularly at low application rates.
MilF specification’s test nozzle more accurately represents military nozzle performance and crash truck foam qualities. ICAO uses a hand-made UNI86 test nozzle, greatly exceeding most ARFF foam branchpipe performances, where poorer aeration and lower foam stability is normal.
Important supplementary and environmental properties (potentially causing problems after purchase) are rigorously tested by MilF specification’s tight acceptability requirements, many of which F3s seem unable to meet. ICAO Levels B and C have no similar tough requirements. Corrosion, fish toxicity, biodegradability, oxygen depletion (COD/BOD) and dry chemical powder compatibility are all tested under MilF specification, which now has a follow-up compliance testing element to assure on-going product integrity, and a residual PFOS/PFOA test requirement at maximum 800ppb (for each). All absent from the ICAO requirements, where potentially blended agents with undesirable component levels are not tested, so cannot be detected or rejected. Stability testing for 10 days at 65°C before fire testing, plus a fire test of mixed qualified concentrates together, is also required to extinguish within MilF specification criteria. Approved products are Qualified Products Database listed1. This rigor provides valuable assurance of reliable performance, product stability and long-term storage when MilF specification approved concentrates are selected. All current generation F3s cannot be mixed together or with AFFFs in storage according to manufacturer’s recommendations, which may create problems of sole sourcing, product unavailability, or incompatibility across mutual aid agreements.
NFPA 403’s latest 2018 edition accepts equivalency of MilF specification and ICAO Level C, without any clear justification. It increases ARFF response times to three minutes (50 per cent longer), despite no change to the critical rescue firefighting access area, rapid response area, or stated survivable atmosphere times inside a fuselage fire. It also accepts usage of F3 (defined as fluorine free synthetic foam (FSFF)) which should be UL listed (requiring higher application rates), plus annual testing according to NFPA 412:2014, despite no definition of F3 foam quality requirements. Any qualified U.S. MilF spec, or ICAO Level C certified foam requires UL listing. Why?
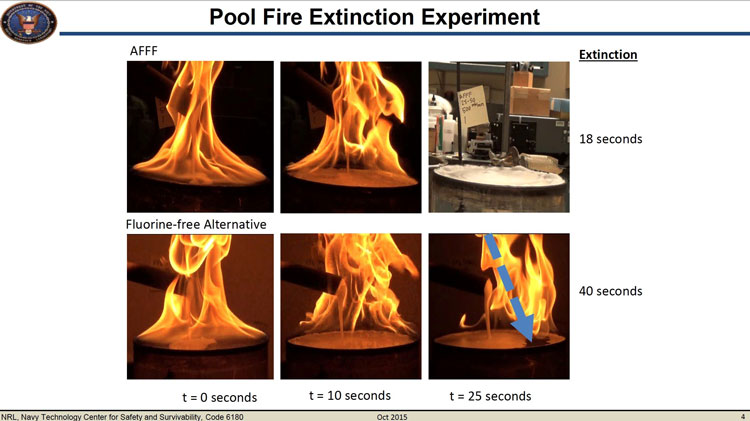
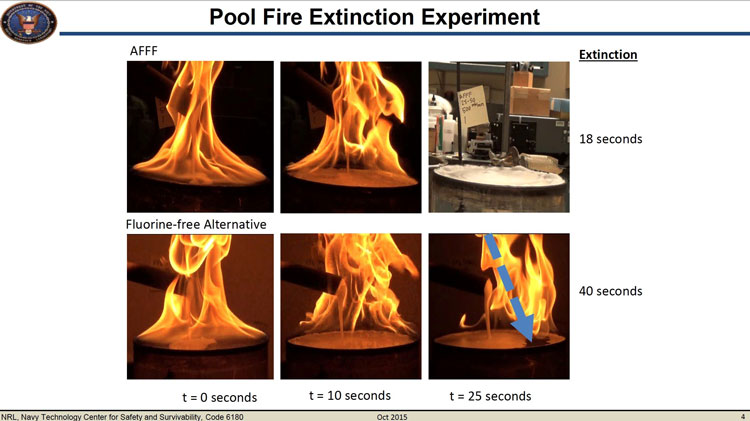
Comparison of AFFF v fluorine free foam extinguishment on same n-Heptane pool fire – U.S. naval Research Lab (NRL) 2015
Ambient temperatures and conditions
Superficial similarity declines when ICAO testing requires relatively low ambient temperatures (≥15°C), hardly representing summer in most places, or year round in tropical areas. The MilF specification is not perfect either, but benchmarks test temperature at 23°C, with acceptability 17-28°C. With global temperatures set to rise, shouldn’t we expect any fire test standard to also be conducted representing summer at say 35°C, verifying reliability?
A 2016 F3 demonstration to ICAO Level B (why not Level C?) in Singapore was hurriedly switched to C6 AFFF because “too many environmental factors were not under our control to do F3”. Reportedly the day before F3 twice failed this Level B fire test, igniting the fuel separator displaying poor fire control. The C6 AFFF demo provided effective, reliable fire control and extinction, as expected. Why not F3? Three weeks earlier a major Boeing 777 engine fire at Singapore, was extinguished in two minutes using fluorinated AFFF/FFFP prior to safe evacuation of all 241 passengers and crew onboard.
Some certificated ICAO Level B (and potentially Level C) approval tests were conducted at 0°C with fuel at 5°C – failing test criteria. Cooler temperatures decrease fuel volatility, while increasing foam stability, making it easier to pass. In Dubai in 2016 a Boeing 777 aircraft fire continued burning in 48°C ambient conditions, until the aircraft was destroyed, despite a concerted foam attack. Miraculously all passengers and crew evacuated before foam delivery to a developing fuel fire. A brave firefighter tragically lost his life in a fuel tank explosion after nine minutes. Extensive foam application continued, but full fire control was not achieved until 16 hours after impact. F3 is reportedly used by the largest Middle East airport. Was it used in this incident or not? Over two years later we are still awaiting the final investigation report to find out.
Fast reliable extinction and dependable safety margins prevent escalation, protecting lives from varied often unknown factors that may intervene, making emergency incidents more difficult. These include high winds, torrential rain, high temperatures, hidden ignition sources, unpredictable explosions, incandescent materials, heavy traffic, human error, equipment malfunctions plus secondary hazards representing just a few ‘what if’ possibilities, potentially impeding successful incident rescue/extinction. Product capability, safety margin, training, all help make that difference between success and failure.
Speed, effectiveness and reliability
MilF specification focuses on fast, effective control and extinction, requiring the smaller test extinguished within 30 seconds (three per cent induction); 45 seconds (half strength), 55 seconds (over-rich with seawater) and 50 seconds for larger 1. 64L/min/m2 test with seawater. Sharply contrasted since 2014 when ICAO doubling previous ≤60 seconds requirement, allowing 120 seconds for full extinguishment – edge flickers being a sign of flashback vulnerability.
Compelling testimonies from two leading F3 producers to U.S. Washington State House Environment Committee highlighted critical problems and likely adverse consequences, if a blanket PFAS ban was enforced, as happened January 2018 in South Australia. They explained: “Use non-fluorinated foams where ever you can but maintain the short chain chemistry AFFFs and AR-AFFFs that need to be used for critical situations like aircraft rescue firefighting and large catastrophic fuel-in-depth type fires. “Once you get to a situation where the foam actually has to plunge below the surface because of the application techniques, the fluorine free foams actually pick up some of that fuel and by the time the foam comes to the surface after plunging below it, it actually burns”.
Why are we allowing inferior AFFFs and most F3s which previously failed ICAO Level B, to now pass? How does that improve life safety for anyone?
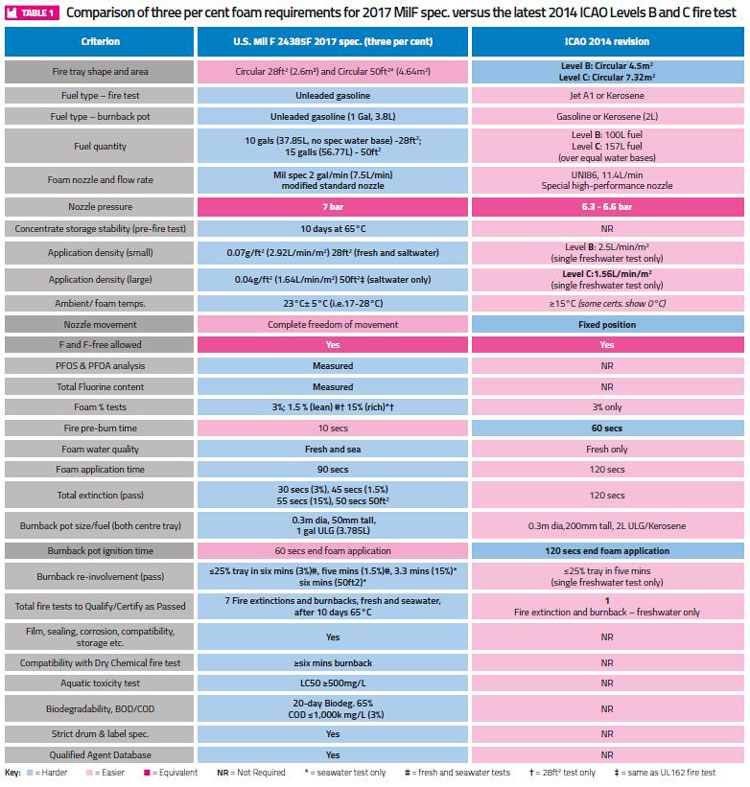
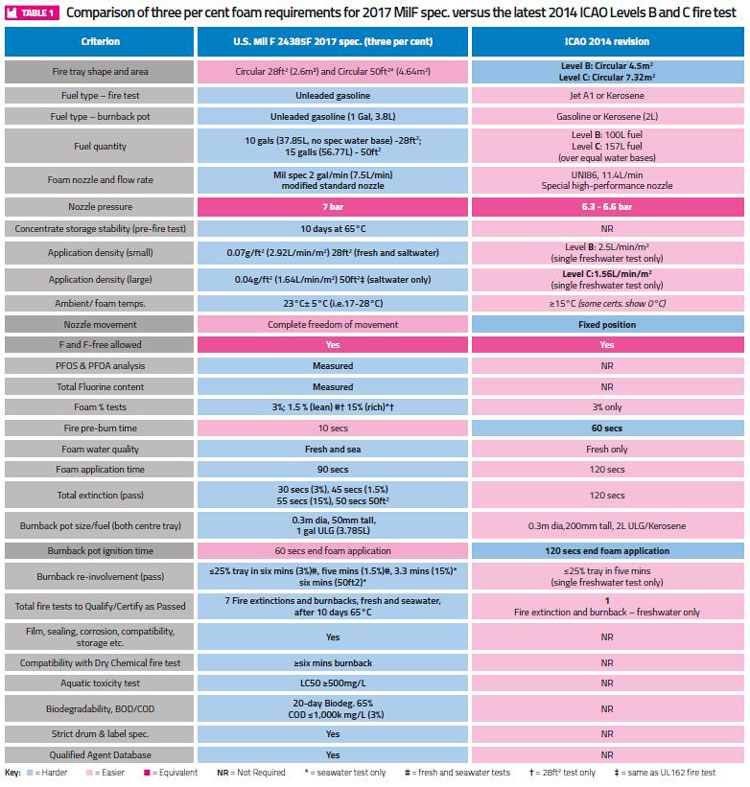
Table 1: Comparison of three per cent foam requirements for 2017 MilF spec. versus the latest 2014 ICAO Levels B and C fire test
MilF specification – F3 goal – beyond the minimal
The U.S. MilF specification aims beyond the minimal, probing potential and evident problems that could occur in the line of duty. Driven by a desire not to repeat the 1967 USS Forrestal disaster, when 134 servicemen tragically died, 161 were injured, 21 planes destroyed and 40 damaged. The fluorine-free foam usage in this incident hastened the development of effective AFFFs. The foam had multiple agency approvals, but no inherent fuel repellency or film formation. MilF specification minimises risk of failure – before approval, providing regulators and foam users robust confidence of effectiveness and reliability to save lives. Crucially AFFF performance was verified effective on large scale fire tests (up to 3,000m2), upon which most system design standards are now based. Why aren’t F3s similarly verified on large fires, confirming robust effectiveness?
MilF specification’s 2017 declared objective was to “acquire and use a non-fluorinated AFFF that meets performance requirements of U.S. Department of Defense, which it is researching to that end, but a viable solution may not be found for several years”. AFFF manufacturers and vendors are encouraged to reduce PFOS, PFOA, and other PFAS levels in their products, driving them toward zero, while still meeting MilF specification requirements. The United States Air Force spent $US 6.2 million replacing legacy C8 foam stocks with C6 AFFF in 2016. More C6 for large fixed systems followed. Any notions of ICAO level C “equivalency” to U.S. MilF specification seem dispelled.
Is ICAO’s dilution serving public safety?
In my opinion, probably not. Particularly when any foams unable to quickly prevent all flames near aircraft evacuation points, should be treated with distrust – a sign fuel shedding and rapid vapour sealing abilities are lacking. Their criticality in AFFFs and absence in F3s was verified by 2012 U.S. research, confirmed by 2015 Naval Research Labs. Absence potentially leads to unpredictable or sudden flashbacks, rapid foam blanket destruction and re-involvement. It happens with poor quality AFFFs and F3s particularly when applied forcefully to volatile fuels, and fuel in-depth fires (≥25mm depth). Small-scale testing, extensively verified by large-scale tests (≥ 3,000m2 fire area) for AFFFs and other fluorinated foams, confirmed equally low application rates achieved. Is this true of F3s?
Interestingly, airport fire chiefs and senior managers currently using F3 agents seemed unable to identify any significant aircraft fire incident where F3 was used, irrespective of success. Should we be raising greater concerns for passenger safety when potentially poorer quality AFFFs and F3 agents now protect ICAO-regulated airports, endorsed by NFPA 403?
Biography
Mike Wilson graduated as an environmental scientist and has over 30 years of experience and specialist knowledge of firefighting foams, their development, systems, testing, differences, applications, fire performances and environmental impacts, for both fluorinated and fluorine free agents and their application systems.
Issue
Related topics
Aircraft rescue and firefighting (ARFF), Airside operations, Safety