Handling the A380
- Like
- Digg
- Del
- Tumblr
- VKontakte
- Buffer
- Love This
- Odnoklassniki
- Meneame
- Blogger
- Amazon
- Yahoo Mail
- Gmail
- AOL
- Newsvine
- HackerNews
- Evernote
- MySpace
- Mail.ru
- Viadeo
- Line
- Comments
- Yummly
- SMS
- Viber
- Telegram
- Subscribe
- Skype
- Facebook Messenger
- Kakao
- LiveJournal
- Yammer
- Edgar
- Fintel
- Mix
- Instapaper
- Copy Link
Posted: 10 June 2005 | Dr. Thilo Stilp, Manager Ground Operations & Environment, Airbus, A380 Program | No comments yet
Although in the past airlines have been more involved in the design an active dialogue with ground handlers and suppliers has ensured an easier entry into services, writes Dr. Thilo Stilp.
Although in the past airlines have been more involved in the design an active dialogue with ground handlers and suppliers has ensured an easier entry into services, writes Dr. Thilo Stilp.
To the 15 customers that have already decided to add the A380-800 or its freighter version, the A380-800F, to their existing fleets and the 60-plus international airports that are going to welcome the A380 by 2010, the first flight of the A380 sets the date at which their preparation for the commercial entry into service of this aircraft enters the active phase.
Airlines are traditionally more closely involved in the design of a new airliner compared to airports and the ground handling community, who are usually confronted with the outcome of the airliner’s dialogue at a later stage of the process. The airport’s and ground handling community’s role of ensuring the highest level of operational reliability right from day one often goes forgotten. Not so with the A380. It was recognised from an early stage that input into the design from the airports and ground handlers, as well as the airlines, would be essential to ensure a seamless entry into service.
The compatibility dialogue
Since the mid 1990’s, when the A380 was still known as the A3XX, Airbus has actively worked with the major airlines, airports, ground handlers and regulatory authorities and international standardisation bodies to ensure that their comments would be considered. The result has been essential for optimising the aircraft with respect to ground handling processes and equipment.
As a result, all of the airports that have received firm declarations from airlines of their intent to operate the A380 are ready today or actively preparing their infrastructure for accommodating the aircraft. Many more have included the A380 in their planning process.
Providing early and reliable information on the design process and the aircraft characteristics was considered key to allowing airports and the ground handling community to start their planning and preparation process at the earliest possible stage. The so called ‘A380 Airplane Characteristics for Airport Planning’ manual was issued in its first version as early as February 2001. Since then the document, freely available via the Airbus web page (http://www.airbus.com/product/a380_introduction.asp#), has been frequently updated and complemented with new data.
In addition, a dedicated A380 ground operations team entered into close dialogue with airline operators, ground handlers and ground handling equipment manufacturers. This team has provided a focal point for the entire ground handling community regarding all aspects of A380 ground handling. The industry’s expectations regarding the new aircraft’s ground handling capabilities were captured in a series of questionnaires and numerous meetings. The team then ensured that these expectations were captured in firm design requirements for the new aircraft.
Through early contact with industry standardisation bodies such as SAE and ISO and with active participation from the IATA Ramp Service and Equipment Group, as well as other industry working groups, the team ensured that the A380 was considered in the revision of existing, or the creation of new industry standards and recommendations. For example, the ISO/SAE standards for tow bar design and tow bar-aircraft interface (SAE – ARP 1015 B, ISO 9667 and SAE – SA 1614, ISO 8267, respectively), the new IATA AHM 926 (Functional Requirements for an Upper Deck Catering Vehicle), update of AHM 904, to name just a few.
Servicing and simulation
As a result of this rigorous consultation process, the A380, despite its full-length, wide body upper deck, can be handled like any other wide body aircraft.
Position and servicing heights of ground connectors such as electrical connectors, high and low pressure air connectors, potable and waste water service panels, refuel connectors and refuel service panel are comparable to those of existing wide body aircraft and can be reached with the same equipment that is already in service at airports today such as the 747-400, 777-200, A340 and A330 -. All connector types are standard and well known from the current Airbus wide bodies.
The position of doors on the main and lower decks has been carefully selected to allow all servicing activities to take place simultaneously. Doorsill heights of lower deck cargo doors, main deck and upper deck passenger doors are equivalent to those of a 747-400 in order to ensure compatibility with existing GSE. Equipment count is also similar, the A380 requiring 21 pieces of GSE, compared to 20 for the 747-400. Of these 21 units, only the upper deck catering vehicle and tow tractor need to be specifically A380 capable.
All of the interfaces for the ground handling and servicing equipment for the aircraft were designed using high fidelity 3D simulations. To this end a new simulation tool especially dedicated to the aircraft ground handling process was applied to the A380 for the first time. In order to allow detail verification and optimisation of the physical and human interfaces during the aircraft’s turn-around a simulation based on the digital design data not only of the aircraft but also of the interfacing GSE was necessary (see figure 1). At this stage special credit should be given to the numerous GSE manufacturers who were willing to provide Airbus with the detail design drawings of their latest product. These made it possible for proposed aircraft design solutions to be analysed in a virtual reality environment and for potential interferences between aircraft and interfacing GSE to be identified early on in the design stage. Built on a process oriented software platform the tool also allowed the study of the full aircraft, the study of time-based turn-around and supported airlines and ground handlers in optimising their operational processes.
A380 turn-around time
Not surprisingly, when entering into commercial operation in 2006, the A380 will mostly be operating on the same routes that are currently served using 747-400 or other wide body aircraft.
Many airlines are planning to integrate the A380 directly into their current network.
Taking full benefit of the productivity step change of the A380, with its seating capacity of 555 passengers (35% higher than 747-400) means that the A380 should be handled within the same time constraints as today.
Observations performed by Airbus between 1994 and 1995 and an airline survey carried out in 1997 on turn-around times achieved with the 747-400, revealed that typical times for a 747-400 operated on international routes ranged between 75 and 180 minutes. In fact the majority of observed turn-around times were clearly beyond the 90-minute limit. Meeting the 90-minute turn-around time requirement therefore became one of the critical design parameters of the A380 (see figure 2).
For most wide body aircraft the critical paths in the turn-around process are usually the boarding and de-boarding of the passengers and the catering that has to take place in-between.
It has become a well-established myth that in order to ensure competitive turn-around times for the A380, airports need to provide at least three passenger bridges. This is simply not the case.
In fact, the time required for boarding and de-boarding the A380 via passenger bridges connected to door M1L and M2L on the main deck will be similar to the B747-400. While this may be surprising at first, it can be easily understood when looking at the A380 interior layout in comparison to that of a B747 (Figure 3). For both aircraft the critical path during the boarding process is the boarding of economy passengers via door M2L. As both aircraft offer about the same number of seats aft of door M2L the time required for boarding and de-boarding is the same. In fact computer simulations have shown that due to the larger aisle width offered by the A380 and the unobstructed access at door 2 (the narrow stairs of the 747-400 create a bottleneck) the time for boarding and de-boarding the A380 may actually be slightly faster than for the B747.
With the critical boarding path on the main deck, direct access to the A380’s upper deck is not an operational necessity to achieve short turn-around times. However, it does offer significant potential in terms of passenger comfort and product differentiation. For most airlines who ordered the A380, the unique ability to offer their mostly premium class passengers direct upper deck access to the aircraft is of high importance. Airports also realise that the level of service provided to passengers can be a decisive argument in remaining competitive. If an airport currently offers two bridges, the airlines preferred choice is to have one of them upgraded to reach the upper deck.
The feasibility of upgrading existing stands for upper deck access largely varies from airport to airport and depends mainly on the constraints imposed by the existing gate layout. The different technical solutions offered for upper deck access were explored in a joint working group of airports, airlines, boarding bridge manufacturers and Airbus. As a result of this open dialogue more than 27 airports are today planning to provide direct upper access either via two or three bridges.
Upper Deck Catering
In contrast to boarding/de-boarding, the direct catering of the galley located at door U1 of the A380 offers a significant gain in turn-around time. Though the A380 is equipped as standard with trolley lifts between the main and upper deck at doors M2 and M5, catering solely to the main deck results in a turn-around time of 126 minutes. Recently there have been comments in some publications that have incorrectly stated that the trolley lifts are not designed for permanent operation; it is worthwhile to rectify the statements at this stage. The recommendation for direct catering of the A380 upper deck (to door U1R) is only due to operational considerations (shortening the turn around time from 126 to 90 minutes) and not in any way related to a technical deficiency of the lifts. Again, the reason why catering door U1R shortens the turn around time can easily be understood by examining the bottlenecks in the catering process. Considering the Airbus reference layout of 555 passengers, which corresponds with the layouts chosen by several A380 customer airlines, the time needed to cater the galley at door M2 will be around 32 minutes . If at the same time the galley at door U1 is catered via the lift installed at the galley M2, the total time for the catering process adds up to around 84 minutes, effectively making catering operations the critical path of the aircraft turn-around. If, however, the galley at door U1 is catered via a dedicated vehicle interfacing directly to door U1R the total time for the catering process is reduced to 36 minutes. Direct catering of other galleys on the upper deck is also possible, but it does not contribute to a reduction in total catering time, as these galleys are not normally within the critical path of the process.
It is evident that direct catering at door U1 allows for a significant reduction of the total aircraft turn-around time while improvements in the boarding and de- boarding through utilisation of more jetways are relatively low.
UD catering vehicles
Vehicles that are capable of catering at the 8m sill height of door U1R are clearly a novelty in ground operation (it should be noted that the other three catering vehicles serving the M2R, M4R and M5R galleys are of course standard wide-body units). After having realised the advantages of UD catering, Airbus was urged by its customers to initiate a dedicated working group in order to establish the technical feasibility and to promote the development of vehicles capable of UD catering at the A380’s door U1R.
In February 2001 the first meeting of the working group involving airlines and Airbus took place. Soon then the group expanded to involve equipment manufacturers and catering companies and since then seven working group meetings have been held with the participation of seven airlines, 14 equipment suppliers and nine major catering companies.
In the course of the working group the technical feasibility as well as the operational and safety requirements for an UD catering vehicle were established and as of today more than eight suppliers are offering UD catering vehicles on the market. Although the design and concept of the vehicles varies with the different suppliers, they are all based on existing proven technology and are all capable of servicing the main deck of the A380 and other wide body aircraft. Airbus supports equipment manufacturers in the testing and operational validation of their prototypes by offering at its site in Toulouse a full-scale mock-up of the A380 fuselage sections dedicated exclusively to the testing of UD catering vehicles. Several manufacturers are expected to take advantage of this unique possibility in 2005.
The working group also strongly influenced the creation of a new IATA AHM 926 recommendation that specifies the functional requirements for an UD catering vehicle and provides an agreed guideline for the industry.
What next?
More could be said about the ground handling of the A380, however the interested reader is referred to the more detailed technical information material mentioned above or may contact the author directly.
For the A380, as for any new aircraft put into service, the final ‘proof of the pudding, will be in the eating’. The A380 will have to prove its compatibility with existing airport infrastructure and processes in daily operation. However the fruitful dialogue established in past years between Airbus, the airports, the ground handling community and the regulatory authorities has served as an excellent means for all stakeholders to be fully prepared for the entry into service phase. The tools and processes developed in the context of A380 will also be further extended to improve the ground handling capabilities of the existing Airbus fleet and to optimise the design of future Airbus aircraft.
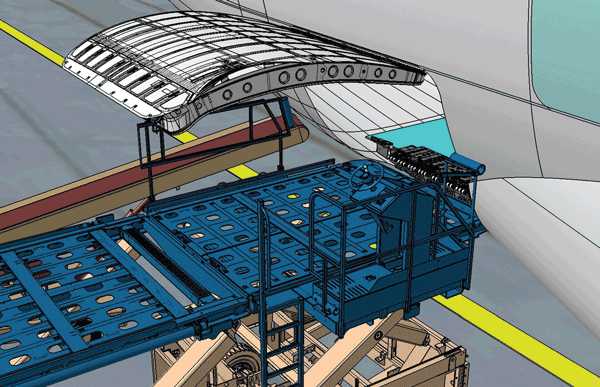
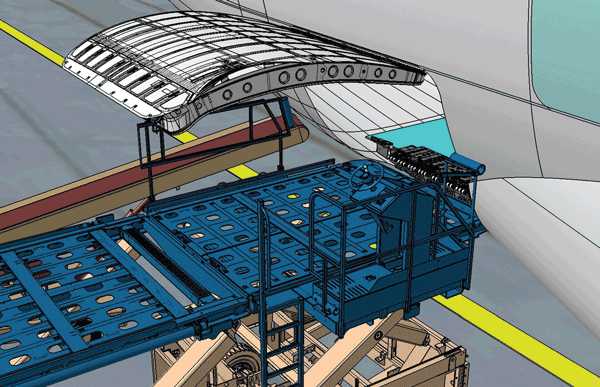
Figure 1: 3D simulations were used during designs
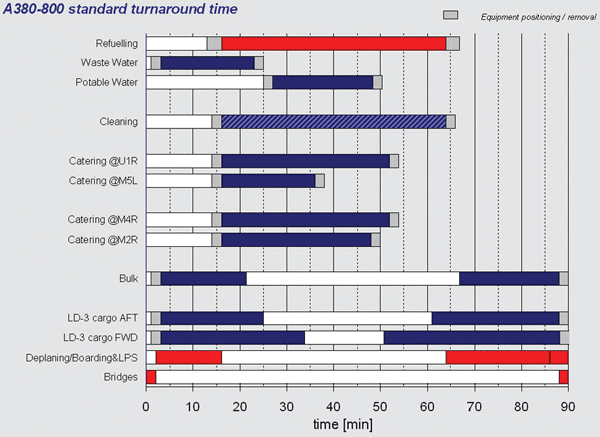
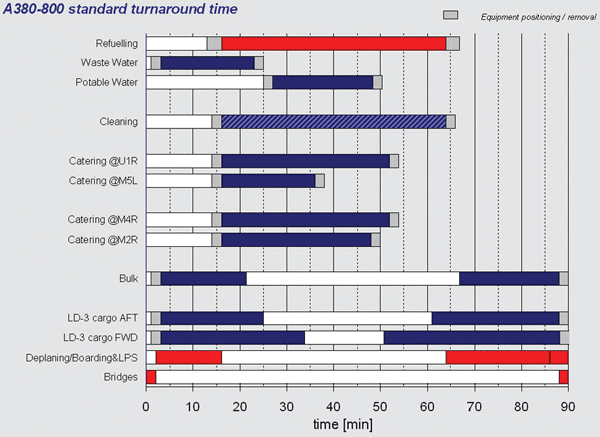
Figure 2
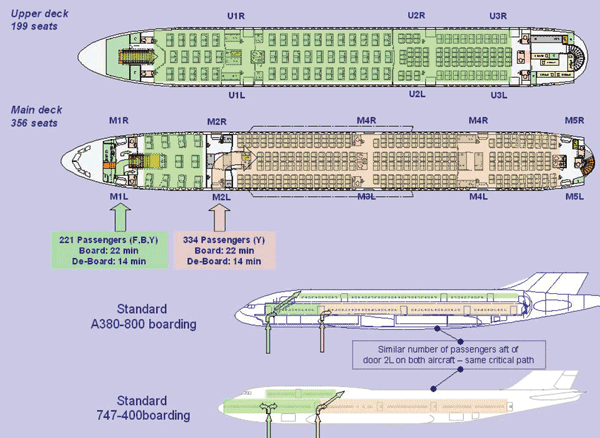
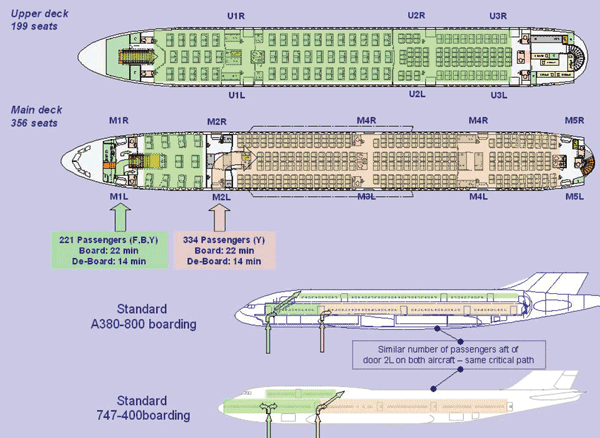
Figure 3
Dr Thilo Stilp
Dr Thilo Stilp holds a a Doctoral Degree in Physics from the University of Heidelberg, specialising in the impact of aviation on atmosphere and climate. Dr Stilp joined the Airbus A380 programme in 2000 as an environment manager responsible for the wake turbulence issues of the A380 after. Since 2001 he has been Head of the Ground Operations and Environment Group within the A380 programme. Email: [email protected]
Issue
Related topics
Augmented reality (AR)/ Virtual reality (VR), Ground handling