London Heathrow Airport: Lighting the way
- Like
- Digg
- Del
- Tumblr
- VKontakte
- Buffer
- Love This
- Odnoklassniki
- Meneame
- Blogger
- Amazon
- Yahoo Mail
- Gmail
- AOL
- Newsvine
- HackerNews
- Evernote
- MySpace
- Mail.ru
- Viadeo
- Line
- Comments
- Yummly
- SMS
- Viber
- Telegram
- Subscribe
- Skype
- Facebook Messenger
- Kakao
- LiveJournal
- Yammer
- Edgar
- Fintel
- Mix
- Instapaper
- Copy Link
Posted: 14 December 2014 | Peter Leeming | No comments yet
Over the past two years, Heathrow Airport has resurfaced its two runways and upgraded its runway lighting to LED fittings. Peter Leeming, Head of Airside Development and Strategic Planning, outlines the mammoth project
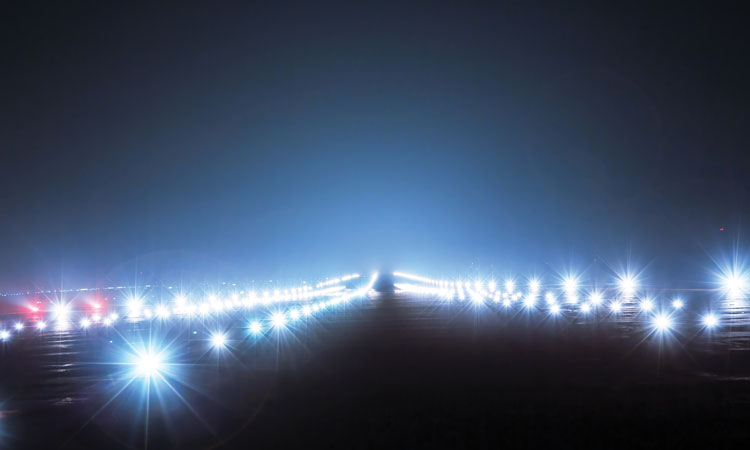
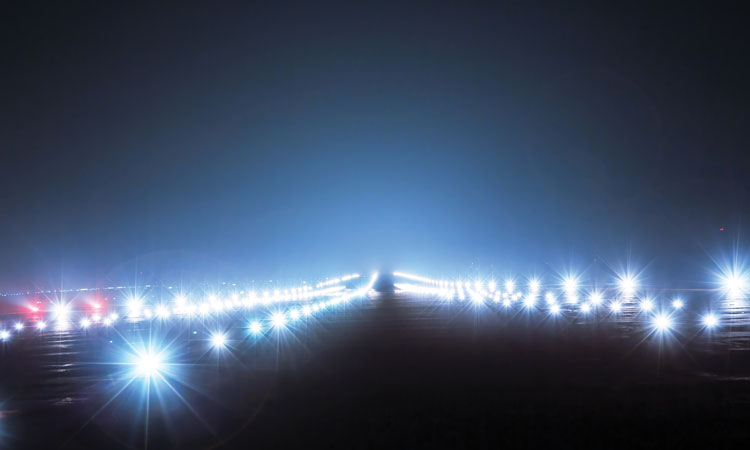
Heathrow Airport is the busiest two-runway airport in the world. In 2013, more than 72 million passengers travelled through Heathrow, a number that is on course to be exceeded by the end of 2014. On 17 August 2014, all records were broken when Heathrow experienced the busiest day in its history, with a total of 241,412 passengers using the airport.
Heathrow’s two runways operate at 99 per cent capacity from 6am to 11.30pm, seven days a week, 365 days a year. Ensuring these two runways are in the best possible condition in terms of safety and efficiency is of paramount concern in terms of maintaining a reliable daily operation and therefore a great experience for each of those 72 million passengers.
Runway refurbishment
Originally constructed at the end of World War II and subsequently extended in the 1970s, Heathrow Airport’s runways need to be refurbished around every 10 years, and this includes replacing the runway surface lighting.
The most recent refurbishment programme is just coming to an end, with the 3,660m southern runway already completed in 2013 and the 3,902m northern runway finished October 2014. Completing this work overnight and ensuring the runway is available for operations by 6am the following morning has certainly been a challenge and has involved much detailed planning and preparation, disciplined execution and collaboration between the many stakeholders involved.
Re-surfacing the runway involved planning out 332,000m2 of the old grooved Marshall Asphalt surface and replacing with the same material. Refurbishing the runway lighting, however, did involve a significant change in that both runways at Heathrow are now fully equipped with LED fittings for centre line, touch down zone, edge, threshold and stop end lights – a total of 1,720 lights changed.
Runway LED lighting: Now a reality
LED fittings for taxiway centre lines have been in use at Heathrow, on a trial basis, since 2002. In 2005 the UK CAA issued an information notice (NOTAL 6/2005) approving the use of LED lights but limited to taxiways only.
As development and refurbishment works have progressed around the taxiway system, around 7,500 out of the 14,300 taxiway lights are now LED fittings. These fittings have already demonstrated much longer life times, lower energy and maintenance costs as well as a very clear and consistent pattern for pilots.
In 2010, the CAA requested that a trial be conducted to prove that the use of LEDs within a high intensity runway application was both technically feasible and safe for runway operations. The trial was managed by the Airport Operators Association (AOA) as part of the technology working group that manages the safe execution of airfield trials and was conducted at Manchester Airport. ADB fittings were used, and following a successful trial, the CAA released an information notice in 2012 approving the use of LEDs in a high intensity application.
Heathrow wanted to see if the same benefits from taxiway LED fittings could be obtained for runway lighting, and Heathrow Airside Operations together with the Heathrow Project Team, worked with ADB Airfield Solutions, Amey and the CAA to ensure suitable approved LED fittings were available, that would meet both CAA and Heathrow requirements.
This work resulted in the runway re-surfacing contract, signed in 2012 with Morgan Sindall as the Principle Contractor (using ATG as the electrical sub-contractor), including the installation of new ADB LED runway fittings.
Tungsten halogen vs LED
Runway lighting deployed in a high intensity application requires strenuous light output characteristics to be maintained – around 10,000 candelas for runway edge lighting, for example. These characteristics (specified within CAP 168) are dictated by regulation and have been established by considering the distance at which the pilot needs to ‘visually acquire’ the lighting as well as distinguishing the runway lighting from other ambient lights.
Traditionally tungsten halogen lamps have been used, mainly because it was the only technology available that met with the requirements, and it had a proven track record spanning nearly 30 years. However, this technology requires frequent lamp replacement as well as relatively high energy consumption to power them.
On average, a halogen fitting utilised as a runway centre line aid, has a life span of around 1,460 hours (or six months, assuming it is being used for eight hours per day). Whilst the lamp itself has a projected life expectancy of 4,500 hours and might still be functional, the degradation to the light output suffered over time deems the light unserviceable in terms of CAA requirements well before the 4,500 hour mark.
At Heathrow, halogen runway lights were changed every six months due to light output degradation, equating to the replacement of approximately 150 fittings per month.
Once the light fitting has been deemed unserviceable, it was then removed and sent back to the workshop where it underwent a full refurbishment before utilisation as a future replacement fitting.
In terms of energy consumption, a halogen runway edge light, for example, also typically consumes 200 watts when on full intensity. In contrast an LED fitting has an expected life in excess of 70,000 hours, a figure backed up by taxiway installations from 2002 still being in operation. In comparison to the 200 watt halogen runway edge light, the LED equivalent only consumes 60 watts at full intensity and all the light is directly utilised.
Overall, the Heathrow Airfield Engineering teams are now saving approximately 7,000 hours of maintenance activity and £118,000 in terms of energy costs per annum as a result of the move to LED fittings.
Runway lighting design
Amey undertook the design for the runway resurfacing project including the runway lighting and, in conjunction with Heathrow, specified ADB Airfield Solutions’ AD-Lights. This was primarily due to the success of the taxiway equivalent on the airport since 2005, but also because ADB luminaires had been the preferred light fitting at Heathrow since 2001, old seating rings could be re-used as they were compatible with the new ADB LED fitting.
Selecting ADB’s constant current version of LED fittings also meant that a straightforward retro-fit was possible, thereby enabling the airport to use some of its existing infrastructure.
The full power savings from LED fittings will only be realised when the existing MCRs (Microprocessor Controlled Constant Current Regulators) are replaced with APUs (Advanced Power Units). The pre-existing 6A primary circuit currents for taxiways and stop bars and 12A primary circuit currents for approach and runway services at Heathrow are a legacy from the Air Ministry days (RAF aerodromes also use 6A and 12A circuits).
Although various primary circuit currents have been used (including 8.33A) the de facto world standard is 6.6A. Both runways have now been converted to 6.6A primary circuits and by gradually converting the circuits at Heathrow to 6.6A, equipment and spares can be bought off-the-shelf leading to lower cost and better availability.
The existing MCRs in the AGL substations, which supply the runway primary circuits have also been either converted or replaced by the manufacturer to 6.6A primary currents.
Installation
There were no changes required in the location of the lights so the new fittings were replaced in the same positions as the old fittings. Since the runway was being resurfaced it was necessary to remove the existing AGL seating pots for runway centre line and TDZ lights prior to resurfacing commencing.
This, in turn, meant that the runway was no longer equipped for Cat III operations and consequently the primary works were scheduled from the beginning of April to 30 September in 2013 and 2014, to minimise the likelihood of requiring low visibility procedures.
Works proceeded in a sequential manner along the runway from one end to the other. Firstly, primary and secondary cables were removed from a section. Once this section was far enough advanced, the existing AGL seating pots were over-cored and a 600mm diameter concrete plug installed. This allowed surfacing to proceed, with a 50mm Marshall Asphalt inlay. Surface grooving was then carried out and finally the new seating pots installed, cabled, and new LED light fittings installed.
Operational impact
At Heathrow Airport, where the twin runways operate at 99 per cent capacity all day, every day, it is essential that both runways are available from 6am. In order to achieve this, each night’s work was meticulously planned to ensure there was sufficient work to maximise the efficiency of the shift, but not too much to put the hand-back of the runway to the operation at risk. A series of go/no go decision points supported this together with multiple contingency plans in case of an unplanned event.
The runway was handed over to the project teams at 10.30pm and returned back to the operation by 5.30am the following morning, to enable first runway movements from 6am.
Operational contingencies were also agreed with the airlines in case of low visibility conditions, in particular taking account of the EU-Ops minima for operating in lower than standard Cat I conditions, although these were only required on one occasion during the entire project for both runways.
Bringing into service
Following a multitude of electrical and functional tests, both runways were handed back to full Cat III capability, newly re-surfaced and with LED lighting before the target dates of 30 September in both 2013 and 2014.
Heathrow Airport now has both runways fully equipped with LED inset lighting providing an extremely clear and consistent pattern for pilots, together with lower energy and maintenance costs thereby meeting all the objectives of the original brief.
Given the complexity of the project and the operational critically of ensuring the availability of both runways during the operational day, it is indeed a testament to all those involved that the runway was handed back to operations by 5.30am every day during the two-year period without exception, and that the project timescales for the completion of both runways were achieved, whilst working within budget.
Key learning
Having undergone the experience of changing all the lights and re-surfacing both runways at the busiest two-runway airport in the world, what are the key learning points to the successful delivery of such a critical project? There are many, but the four most important are:
- Planning: Do as much planning as you can both at project level and on a night-by-night basis. This includes dress rehearsals, nightly procedures, contingencies, phasing of the works and the like, as well as the pure technical design
- Collaboration: This sort of project involves numerous stakeholders. Whilst the Airport Operator takes the lead the airlines, ANSP, the CAA, the local community as well as the project teams all need to be involved in the planning and delivery of the work
- Communication with stakeholders: This ties closely to collaboration above, but everyone touched by the works needs to understand what’s happening when and how it impacts them
- Disciplined execution of the plan: In the end there is no substitute for good quality, professional and disciplined execution of the plan in this environment.
Biography
Peter Leeming is Head of Airside Development and Strategic Planning for Heathrow Airport Limited. He joined BAA (now Heathrow Airport Holdings Limited) in 1987 and has held a wide variety of roles primarily within the Engineering and Airside Operations functions.
Issue
Related topics
Airfield lighting, Airport development, Airside operations, Runways and pavements