Unpacking airport’s safety evolution
- Like
- Digg
- Del
- Tumblr
- VKontakte
- Buffer
- Love This
- Odnoklassniki
- Meneame
- Blogger
- Amazon
- Yahoo Mail
- Gmail
- AOL
- Newsvine
- HackerNews
- Evernote
- MySpace
- Mail.ru
- Viadeo
- Line
- Comments
- Yummly
- SMS
- Viber
- Telegram
- Subscribe
- Skype
- Facebook Messenger
- Kakao
- LiveJournal
- Yammer
- Edgar
- Fintel
- Mix
- Instapaper
- Copy Link
Posted: 19 July 2017 | Wayne Anaka | CEO AVCON.WW | 5 comments
President and Chief Executive of safety consultancy AVCON.WW, Wayne Anaka, discusses the evolution of safety management systems in aviation ground operations and considers how the integration of safety management into the corporate and departmental culture could revolutionise the safety industry.
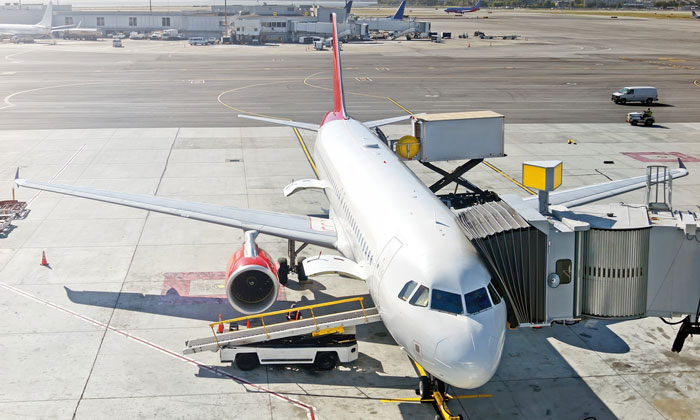
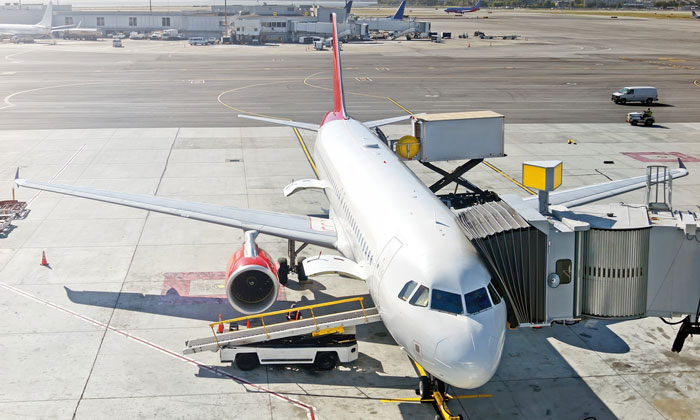
Why does the industry spend so much time and money on safety management training and procedures with little in the way of return?
The monetary cost of aircraft damage alone is estimated to be between $1,000,000,000 (€940 million) and $5,000,000,000 (€4.7 billion) per year. The actual figure depends on whether you are a ground handler or an airline. Ground handlers calculate the cost of the damage and repair, while the airlines add the cost of lost revenue from aircraft being out of service and passenger costs such as rebooking, delay compensation and added fees. When one adds ground equipment damage, personal injury – and especially fatalities – the cost can almost double to $10,000,000,000 (€9.4 billion). These numbers have captured the industry’s attention and most airports, airlines and ground handlers have introduced some very good safety management system (SMS) practices in order to reduce accidents and the associated costs.
There has been positive improvement over the past five years, especially among emerging economies and non-IATA air carriers where regulations and safety programmes were virtually non-existent prior to 2010. Other than the very positive virtual elimination of fatal accidents, the reduction of overall accidents through this period for IATA carriers, while overall still better than the non-IATA carriers, has been stubbornly rather flat.
The aviation industry has better programmes in place promoting safety than ever before. The auditing procedures are excellent. Safety manuals are available in every operating department of most companies. Well trained and motivated ramp safety inspectors exist at almost every airport. Airports have airside vehicle operating permits (AVOP) programmes inclusive of driving tests and demerit enforcement. Airside roadway systems and driving regulations are in place. Signage clearly marks runway and taxiway thresholds and vehicle crossing points. Lifting at check-in counters has been reduced with conveyor systems improved to make lifting less onerous.
The industry holds multiple safety conferences and training workshops worldwide annually. There is clearly a strong effort being made, supported from the top, to resolve safety issues and costs. Insurance companies supply copious amounts of risk analysis information outlining the root causes. Regulators are active in follow up and enforcement, where required. In view of all this, why are we not seeing better results?
Root causes
There are still many areas where further improvement needs to be made. The following pinpoints the main causes of safety issues:
- Lack of focus by operators’ drivers and support staff causing avoidable accidents.
- Staff shortages – especially in severe conditions where staff numbers need to be increased, not reduced. This condition is primarily the result of low wages combined with less than ideal working conditions causing recruiting issues and high turnover and absenteeism. This is especially prevalent in established economies where the competition from outside the industry is intense. Security regulations including the five-year background and or residency requirement impacts the qualified employment pool available. Ground handlers, and to a lesser extent airlines, struggle to maintain their required numbers of employees especially in the ramp and aircraft cleaning departments. Airports are not immune from the competition for qualified candidates but their superior compensation package is at least commensurate with outside industry.
- The staff shortage problem leads to a second area of concern; excessive overtime leading to distraction and fatigue with its inevitable reduced cognitive capacity to function at peak performance levels. This is an area just recently being studied and addressed as it may be a larger contributor than previously understood.
- Ramp congestion with equipment and aircraft movements ever increasing, maximising gate utilisation and ever increasing equipment requirement, leaving parking and staging locations over-crowded, further exasperates safe working conditions.
- Driving conditions deteriorate in inclement weather including slippery ice and snow covered ramps, reduced visibility from snow, rain and fog and poor lighting conditions.
- Pollution from equipment exhaust creating health hazards, not to mention environmental concerns.
- Oversized and heavy baggage needing handling both at check-in and in the baggage makeup area.
- Lack of buy-in to SMS procedures.
- The biggest current challenge – on-time performance (OTP). Delays cost money and the focus on OTP is extremely intense. Employees soon learn that they will receive far more grief from their managers for delays than they will from breaking or bending safety rules and procedures (provided they are lucky enough to avoid an accident).
- Finally, the future challenge of automation and technical advances such as:
- Self-driving equipment
- Fully-automated baggage sortation
- The elimination of checked baggage through door to door pickup and delivering removing baggage from airports all together
- Passenger self check-in and boarding
- Robotic loading machines or artificial intelligence.
There are of course more areas where improvement is needed but in my opinion the above 10 are the most prevalent. And all are driven by lack of, or poor execution of, SMS procedures.
Improving employee focus will always be a challenge as we are all human and not perfect. Every SMS programme addresses procedures to deal with hazardous and congested conditions. Most do not directly address staff shortages, or the need for revised operating procedures resulting from this lack. Equipment congestion and driving are addressed in most SMS programmes, as is oversized and heavy baggage handling with proper lifting techniques and requirement to seek assistance. Some programmes address the pollution concern but many leave this to the environmental planners. OTP issues are swept away with the catch all slogan of ‘safety first’ and the SMS will clearly state this. Unfortunately, the reality is that OTP is really king and the clear focus of management and safety only becomes the priority after the accident or near miss occurs.
I am not currently aware of an SMS programme that addresses point 10, but I am confident the very creative and intelligent people and companies that produce the current programmes are looking at the future ‘what ifs’.
How do we change the current root causes that produce the roadblocks to significantly reduce industry accidents? How do we prepare for future automation and technical advances requiring a different skill set for the current employees to master? How do we get buy-in to safety and change when employees are afraid of being downsized?
Solutions
The answer is the integration of safety management into the corporate and departmental culture. It will require weaving the safety management programme into the standard operating procedures (SOP) so that they become inseparable entities. Everything they do will incorporate ‘safety first’. The process will begin with:
The discovery
This is where the examination of what is currently being done is reviewed in detail and will involve every department that touches on the process:
- Operations who perform the functions from the senior manager to the employee performing the tasks
- Sales who sell the product so they are in sync with operations on deliverables, timelines and costs
- Finance who need to analyse the cost and the expected return on investment (ROI)
- Administration and operations support to ensure they are delivering the right assistance how and when required
The plan
Using all the participants’ individual and collective input, the plan will be developed and agreed upon with specific deliverables including the timeline assigned. This is achieved through a joint statement of work (J-SOW). The J-SOW will involve all departments’ input to synchronise everyone’s understanding of the ‘why, what and how’ – looking at the purpose; what is needed including clearly expressed goals of what success will look like; and how it will be achieved; defining everyone’s roles and responsibilities, the timeline and ROI.
Critical to the success of this integration is the Chief Revenue Officer (CRO) – if there is a measurable and achievable financial gain in the plan then buy-in and focus will be supported from the top. Once everyone is agreed on the purpose, their roles and responsibilities and how this will be achieved, and the budget is in place, then we will move to the next step – implementation.
The implementation
This phase involves ‘best practice’ training and listening to hear concerns and resolve any perceived roadblocks to the buy-in of the entire employee teams. Buy-in is critical to the success of the programme – without it you will fail. This phase is time-consuming but well worth the effort. Once buy-in is accomplished, the development of the operating procedures incorporating manpower and equipment requirements and appropriate adjustments for changes to cover any known contingency plan for staff shortages and equipment breakdown, will move quickly and the employee input will surprise you with their creativity and practicality. If at this stage a previous unknown comes to light, then it may be necessary to return to the plan to revise it to encompass the change.
The evolution
This final phase happens once the plan has been successfully implemented with buy in and will ensure the plan is being executed as designed and correct or adjust to any variances that occur. These will encompass automation, new technology, location and services. There are also analytics being produced today to examine the root cause of lapsed focus and judgement and predictive behaviour indicators that every future SMS programme should ideally address. It is in this phase that the CRO will prove their value many times over. This person can be from the consulting or training team, or internally. The CRO will ensure the plan continues to be executed and enhanced as new procedures and technology are perfected and introduced.
Conclusion
The future of SMS and accident cost reduction will be dependent on successful integration of the SMS programme into the operating culture and CRO thinking to find the cost of chaos and solutions to generate an ROI through accident reduction. This will produce a more productive workforce and an improved bottom line.
Wayne Anaka is currently President and Chief Executive of AVCON.WW, a ‘Best Practices’ training and consulting firm specialising in safety and environment culture in the transportation community. Wayne was the principle founding partner of NavStar Aviation Group, an aviation ground handling company based in three airports in Canada and three airports in Florida. Prior to this he spent 39 years in various management positions for Servisair Canada and Wardair Canada. Focusing on ground handling, winter operations, environmental storm water management, aircraft de-icing, and airline operations and customer service, Wayne was accountable for annual budgets exceeding $50,000,000 and the oversight of over 2,000 people in multiple North American airports. As Director of Operations Support, Wayne oversaw the implementation and training of Sabre Systems, Operating procedures and Quality Assurance. Wayne is CRO certified with extensive knowledge and experience of safety and environmental management systems and sustainability.
Related topics
Airside operations, Augmented reality (AR)/ Virtual reality (VR), Safety
Excellent article Wayne, I believe you have nailed the root causes of safety issues aviation !! The solutions you point out ; the discovery , the plan, implementation and evolution all make sense.
I believe SMS needs corporate culture and corrective action this will only happen if you have the CEO and CRO believers and promoters of SMS.
A well-written article with some hard truths about safety at airports today. For Safety to be integrated into the work culture today, it is imperative that senior operational management undergoes similar training as the front line staff to identify daily challenges, update processes and allocate funds where needed. Availability of GSE or condition of GSE is another factor that requires different approaches to ensure safety is not compromised.
Great article! Clearly lays out the key issues and what has to happen to begin to deal with them. Culture change takes significant resources but most of all, as Mr. Anaka says, it needs constant and committed focus by managers and leaders. Thanks.
Wayne,
The combination of changing our view from the activities and challenges in the existing transportation silos to an industry culture built on the enterprise mission for profitable safety is game changing.
That along with the recognition of the revenue generation advantages from a traveler engagement model that delights the traveling public based on safety and lower cost should start a conversation that leads to change.
Thanks for the observations and sharing the path.
Rick
Fine article! Good listing of core causes of safety issues. It is clear that the safety management in aviation industry still has lot to develop. I believe advanced technology will be a game-changer, also a better safety culture should be practiced by both management and staff.