Friction Testing: In search of better measurements for improved safety
- Like
- Digg
- Del
- Tumblr
- VKontakte
- Buffer
- Love This
- Odnoklassniki
- Meneame
- Blogger
- Amazon
- Yahoo Mail
- Gmail
- AOL
- Newsvine
- HackerNews
- Evernote
- MySpace
- Mail.ru
- Viadeo
- Line
- Comments
- Yummly
- SMS
- Viber
- Telegram
- Subscribe
- Skype
- Facebook Messenger
- Kakao
- LiveJournal
- Yammer
- Edgar
- Fintel
- Mix
- Instapaper
- Copy Link
Posted: 2 June 2015 | Frank B Holt
As part of ASTM International Committee E17’s ongoing work to understand and develop standards for friction testing, former Chairman Frank B Holt describes the challenges and the progress being made to harmonise the measurement process across a range of devices…
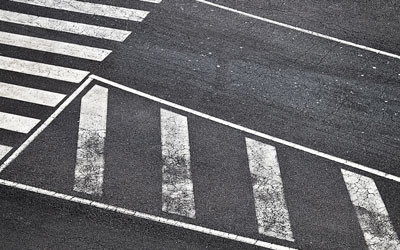
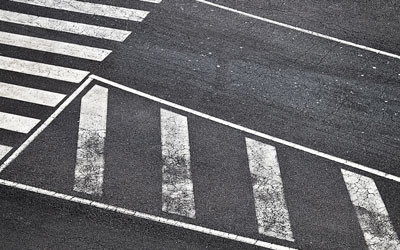
The American Society for Testing and Materials (ASTM) International Committee E17 on Vehicle-Pavement Systems was formed in 1960 to bring together many of the world’s experts in friction and develop standards for data collection, equipment design and data analysis. For example, the committee developed the E274 locked wheel system in a standard form including calibration procedures and water nozzle design. This was a major achievement with most of the 50 States building a variety of machines to achieve the same end – the measurement of pavement friction – which has been a major factor in improving road safety.
For many years there have been multiple attempts to harmonise friction measurements. This has proven to be a most difficult task with many different devices, poor repeatability of some devices, lack of standard calibration surfaces and the lack of a reference device. The NASA sponsored friction workshops which ended in 2008 identified these critical issues and discussions with manufacturers, users and rule making organisations, and indicated the need to continue the work efforts to try and standardise the process for each of the critical items. In 2009 with the support of ASTM International, the voluntary standards organisation joined with the FAA, the Federal Highway Administration (FHWA) and the Larson Transportation Institute at Penn State University to formulate a plan of attack for the issues identified.
ASTM International already had standards for the tires used by the friction devices (ASTM E1551 and ASTM E1844), a generic standard for friction devices themselves (ASTM E2340), a standard for calibration procedures that was used for one of the friction devices (ASTM E556), and a calibration procedure for comparing a device to a reference device (ASTM E2666). These standards already allowed devices to develop better data for use in the FAA circular critical to runway safety. With these standards as a foundation it was determined that the issue of standardised training for operators and identifying and quantifying the differences between devices would be a good start in the process of trying to bring the friction data to a more common ground. The 2009 Friction workshop became a test bed for training material and for the first time allowed a number of devices to be looked at for more than just their Mu values.
Device testing
Like the NASA Wallops Island facility that was used for previous friction workshops, Penn State has a test track which has eight surfaces with a fairly broad range of Mu values varying from low to high. The need for calibration surfaces that are homogeneous, are large enough to collect data and are stable over time could be met with this track. The addition of five other test surfaces at the State College Airport, adjacent to the test track facility, provided additional ranges of Mu and longer straight test sections for greater flexibility in testing some devices. In 2009, 16 devices participated, which provided an opportunity to review equipment and begin to develop additional procedures to fine tune equipment. The number of devices participating each year has remained near this initial number with some new units and a number of manufacturers, owners participating in the work effort.
Targeted efforts focused on measurement of the devices’ load and traction force, measuring how well they measured speed, how they distributed water during testing and development of a process to verify/test the devices.
Like the highway friction testers procedures outlined in E2793 it was decided to test the devices in an ‘as arrived’ condition, then verify and calibrate the unit and perform a calibrated set of tests. Each device ran tests on the various surfaces at the track. Then each unit was put on a calibration platform. The differences in size and shape for the devices provided a number of challenges.
In response to the many challenges of putting different devices on the same calibration platform, a special slab was designed to allow all devices easy access to the platform, so that load and traction characteristics could be easily measured. The calibration platform is recessed into the slab so that the device is kept flat and can be driven or pulled directly onto the platform surface. This provided more accurate information and shortened the time required to check the calibration of the device.
The use of these devices to determine the timing of rubber removal and extent of the runway area to be cleaned is dependent on the accurate placement of water in front of the test tire. The objective is to provide a theoretical one millimetre of water underneath the tire across the width of the tire interface with the pavement surface. Early work on highway devices led to the development of a standard nozzle and a water collection system to determine the distribution and volume of water being delivered by the device.
Initially a device was designed and made of plexiglass to allow the collection of distributed water from a device. Then a mathematical model was used to determine the volume of water delivered while the chambers showed the distribution of the water. This morphed into a grate system mounted in the pavement to allow all devices to traverse the grating, and water was collected in trays allowing accurate definition of distribution and volume.
The real question is still being worked on. Could a standard nozzle and water system be used on all devices to ensure that the correct repeatable volume of water could be applied during testing? The 2015 workshop will continue to pursue this problem.
So one might ask: are we making progress? As presented in the 2012 Workshop report, the condition of devices showed a large variety of results in the ‘as arrived’ condition. Post-calibration efforts found the devices having an average correlation of 0.92 with a standard deviation of 0.02. The report describes that: “The line of agreement representing how close the devices are to true agreement (harmonization) to the measurement of the others went from an average of 64% agreement with a minimum of 43% agreement to a post calibration average of 96% with a minimum of 93%.” 2014 Workshop results showed a similar set of results with a similar mix of testing devices. So indeed the bottom line is we can continue to improve the confidence of users and operators who are making decisions on the safety of their networks, be they roads or airports with improved tools and procedures to embrace the equipment they already have.
The 22nd Annual Friction Workshop is scheduled for August 10-14 2015 at Penn State. The program will include additional testing and refinement of the calibration procedures for the sensors and systems on these devices. The objective is to continue to improve the harmonisation of the devices and provide the best possible data to airport staff for their decision processes.
Biography
Frank Holt is Senior Vice President for Business Development with Dynatest Consulting Inc. where he is responsible for the development of Dynatest’s friction testing equipment. He is a graduate of York University in Toronto, Canada and has spent more than 45 years in the non-destructive evaluation of pavements and bridges including friction, roughness, condition and bearing capacity. He has worked with more than 700 airports and is an active member of TRB Committees AFD10 Pavement Management and AFD90 Surface Properties-Vehicle Interaction. He has been a member of ASTM Committee E17 Vehicle-Pavement Systems since the mid-1970s. He has just completed four years as the Chairman of the Committee and now serves as the Chairman of E17.24 Tires and Sliders. He has published numerous papers in the area of non destructive testing of pavements.