Wind farms and radars living together?
- Like
- Digg
- Del
- Tumblr
- VKontakte
- Buffer
- Love This
- Odnoklassniki
- Meneame
- Blogger
- Amazon
- Yahoo Mail
- Gmail
- AOL
- Newsvine
- HackerNews
- Evernote
- MySpace
- Mail.ru
- Viadeo
- Line
- Comments
- Yummly
- SMS
- Viber
- Telegram
- Subscribe
- Skype
- Facebook Messenger
- Kakao
- LiveJournal
- Yammer
- Edgar
- Fintel
- Mix
- Instapaper
- Copy Link
Posted: 4 April 2013 | Dr Clive A Jackson, Wind Farms Technical Authority, BAE Systems | No comments yet
Credible mitigation options are needed to allow wind farms and airport radars to co-exist. Dr Clive A Jackson, Wind Farms Technical Authority at BAE Systems, explains how harmony can be achieved.
Wind farms are likely to be a significant contributor to the future global energy mix if targets for reducing global carbon emissions are to be met, and as a result, we’re likely to see more on- and offshore wind farms springing up. However, before wind farms can be constructed, they are subject to local and national planning regulations.
In many countries, these require environmental and economic impact assessments. Of particular relevance to wind farms is the potential impact they may have on air safety. Aviation organisations are thus often consulted and may object during the statutory planning process. More than 50 per cent of wind farm planning applications in the UK fail or are significantly delayed due to aviation objections, and similar concerns exist internationally.
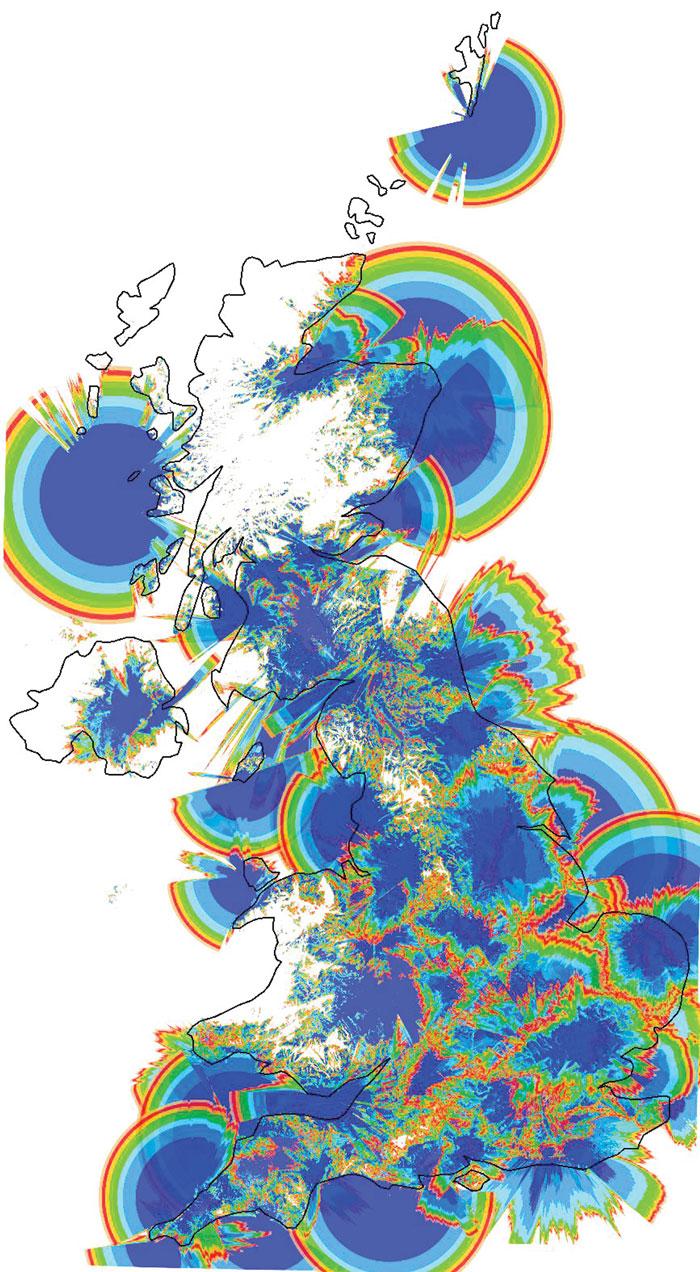
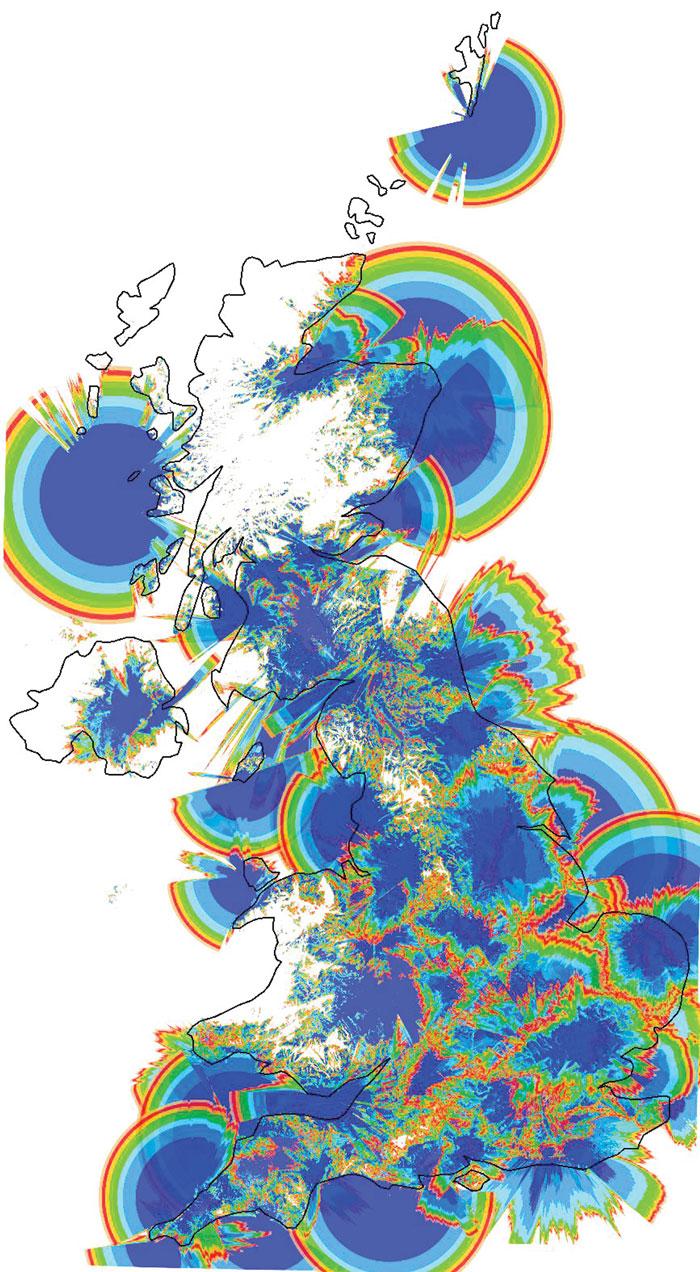
Figure 1: UK radar coverage predicted for
150m-high wind turbines
So why is there so much concern about the impact of wind turbines on aviation? While they can certainly pose a physical hazard to aircraft, this is only generally a problem in the vicinity of airports, when aircraft are at lower altitudes, and does not account for the large numbers of aviation objections. The principal reason is their impact on Primary Surveillance Radar (PSR).
PSRs used for civil aviation purposes are typically capable of detecting moving targets with an effective reflecting area, known as Radar Cross Section (RCS), as small as 1m2 out to a range of 120 nautical miles (nm) from the radar. Radar reflectivity estimates for current generation turbines, including the stationary metal tower, are greater than 1000m2 while the reflectivity of the moving blades, which is contributed to by inbuilt metallic lightning conductors, are of the order of 100-200m2, similar to a large aircraft such as a Boeing 747. This means that, dependent on terrain screening, wind turbines may be detectable by radars out to their full range of operation. With wind farms often being built on high ground or out to sea, where there is little terrain screening, this can expose a lot of potential wind farms to radars (see Figure 1).
Impact on radar
Wind turbine impacts on radars are due to the way they process signals. Most air traffic control (ATC) radars are capable of discriminating between echoes from stationary objects and moving objects on the basis of the ‘Doppler effect’, which largely eliminates the turbine towers as a problem for radar. However, turbine blades move at speeds comparable to aircraft and most ATC radars do not have sufficient Doppler processing capabilities to discriminate moving turbine blade reflections from moving aircraft reflections.
The problem is exacerbated by the fact that most ATC radars only operate in two dimensions (2D, range and azimuth) and are not capable of discriminating aircraft height and therefore cannot eliminate echoes from ground-based moving targets such as turbines. This means that wind turbines are often detected by such radars (albeit intermittently due to the rotation of the blades not being synchronous with the radar).
These radars have typically been designed to deal with large areas of distributed clutter (unwanted returns). They are thus not optimised to deal with multiple large and discrete point clutter sources, such as turbines. This results in negative impacts on radar performance that can have an effect on the ability of air traffic service (ATS) providers to provide an adequate service.
Wind farm clutter
For the reasons already mentioned, wind turbines make ideal, albeit unwanted, targets for radar. This means that radar displays can become cluttered with unwanted and unpredictable turbine returns from wind farms and it becomes difficult for air traffic controllers to differentiate between genuine aircraft targets and wind turbines. Worse still, wind turbine returns may mask or overlap genuine aircraft returns, potentially obscuring conflicting aircraft within the wind farm from the controller. Subsequently, air traffic controllers often direct aircraft to maintain a safe separation distance (usually 5nm) from wind turbine clutter. This can increase track miles flown and thus fuel burnt by aircraft and potentially negate any energy saving benefit of having the wind farm in the first place.
Desensitisation
A more insidious and not immediately obvious effect of wind turbines on radar is desensitisation. This is where the returns from turbines affect the signal processing within the radar in such a way that the probability of detecting a genuine aircraft is reduced. Almost every element of a radar system is vulnerable to wind turbine effects to a lesser or greater extent, however, there are some typical radar system elements that are particularly vulnerable to wind turbine desensitisation. These include front end receivers and analogue-to-digital converters that may be saturated by large echoes from nearby turbines.
One of the most vulnerable elements of a radar system is the detection and clutter suppression processing carried out in the radar signal processor. This usually comprises Constant False Alarm Rate (CFAR) processing that calculates short-term local background clutter strength. If large turbine echoes fall within a CFAR processing interval, they will push detection thresholds upwards potentially above the genuine target level and thus suppress detection of genuine aircraft targets.
In addition many systems also employ Clutter Maps that keep a longer-term record of clutter energy. In older systems, these clutter maps can be quite coarse and have large clutter cells covering significant geographic areas. If large turbine echoes fall into the same clutter map cell as an aircraft then the aircraft detection could be suppressed.
This effect is demonstrated in Figure 2, where genuine aircraft detections have been suppressed in and around a wind farm. So as well as having to deal with a large amount of unwanted turbine clutter, controllers are also potentially deprived of genuine aircraft detections in the areas surrounding wind farms, which has obvious safety implications.
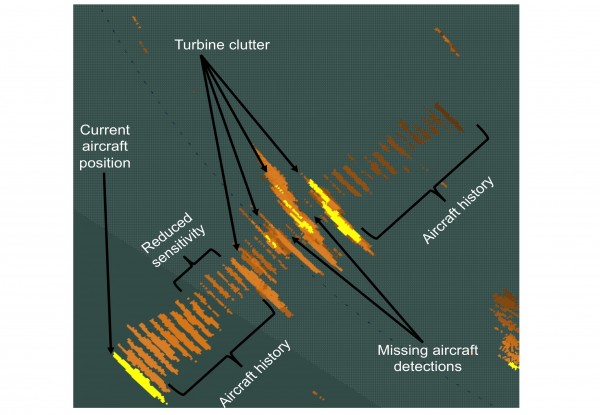
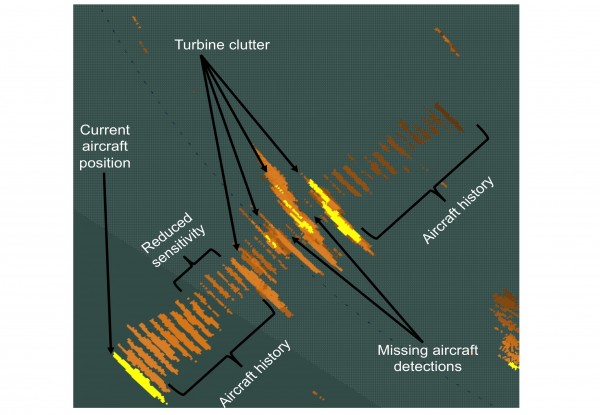
Figure 2: Radar display showing unwanted
turbine clutter and desensitisation to wanted
aircraft returns
Poor tracking performance
While older radar systems tend to use videostyle displays, as illustrated in Figure 2; more modern radars tend to use ‘plot’ and ‘track’ displays (see Figure 3). In these systems detected target location is indicated by markers (plots) and tracking software is used to associate plots on successive scans to form a historical and predicted track. However, large amounts of wind farm clutter detections can cause overload, where some plots are lost due to lack of memory. Along with the already lost aircraft detections due to desensitisation this can cause trackers to lose aircraft tracks, be ‘seduced’ away from genuine aircraft tracks to form a track on a sequence of turbine detections or even initiate new false tracks from turbine detections. This again has an effect on controllers.
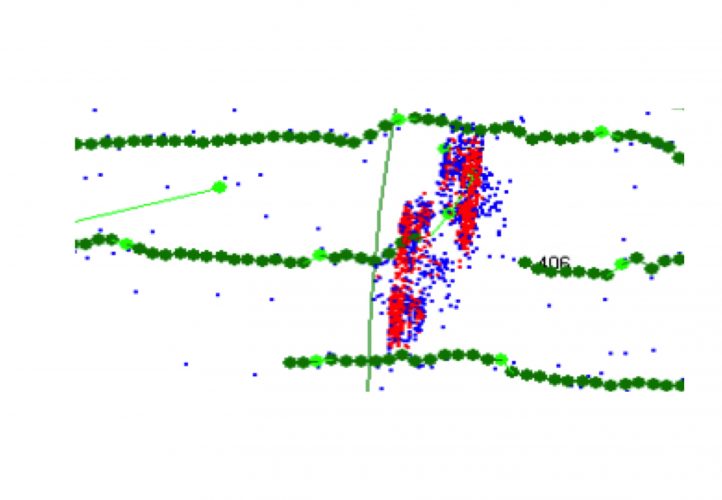
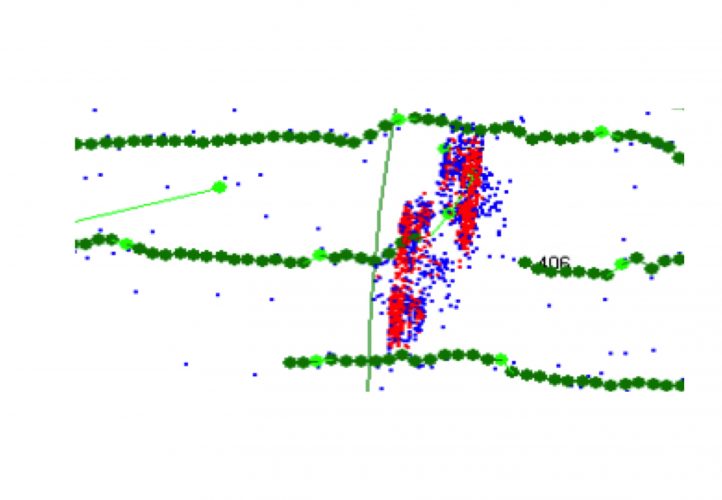
Figure 3: Plot and track time history. Note the number of turbine plots (red and blue) causing the seduction
and loss of the (green) aircraft track in the wind farm before re-initialisation outside the wind farm
Aviation stakeholder response
All of these effects can lead to uncertainty for an air traffic controller and in the worst case can impact on safety. However, since it is their duty to maintain safety, it is more likely that controllers would direct aircraft to avoid any wind farm affected areas with a consequent increase in controller workload and aircraft track miles.
To avoid this situation, ATS providers for both en-route and terminal areas often object to wind farm applications at the planning stage, particularly if the wind farm would be in an operationally sensitive area. While this does lead to engagement and negotiation in the first instance, it often fails and results in deadlock and even time-consuming and expensive Public Inquiries. This can take many months and cost millions of pounds, while at the same time distracting ATS resources away from their principal roles. This also brings considerable risk to both sides if they lose. Wind farm developers may be prevented from building their wind farm or the ATS provider may be stuck with a wind farm in an operationally sensitive area.
With the proliferation of wind farms and large number of existing conflicts during the planning process, this approach is not sustainable. Credible mitigation options are needed to allow wind farms and radars to co-exist.
Mitigation options
So are there any credible mitigation options to manage the problems wind farms cause radars? The answer is yes, and potential solutions are coming to market over the next few years. But these options all have pros and cons:
Infill radar and display integration
To date this is the only proven and operationally deployed mitigation. It is a simple and robust system, with understood risks, but it is an expensive option. The principle of infill is to find an existing radar or position a new radar where terrain screening prevents it from detecting the wind turbines while at the same time providing coverage of aircraft targets at low enough levels to be operationally satisfactory (see Figure 4).


Figure 4: Infill radar principle. Note the need to find appropriate terrain and the residual
lost coverage at low levels
One of the main issues with this option is the difficulty of finding terrain that meets these requirements, particularly if restricted to using existing radars as the infill source. The Whitelee Wind Farm project, the first in the UK to develop operationally deployed infill mitigation, purchased a brand-new infill ATC radar and installed it on a specially surveyed site in Kincardine, at considerable cost to the project.
This approach does carry some risks because the infill site selection must be done via surveying and modelling since it is not possible to build the wind farm before the mitigation is in place. This leads to the use of conservatively large clearances for the infill base of cover above the turbines (to avoid any risk of the infill detecting the turbines) and consequently, although operationally satisfactory, infill coverage is perhaps not as good as possible.
The other drawback of using infill (of any sort) is the need to integrate the data from the infill radar onto the controller displays of the principal radar. This is usually achieved by electronically blanking an area of the principal radar’s display (a mosaic) and replacing the data with infill data (see Figure 5).
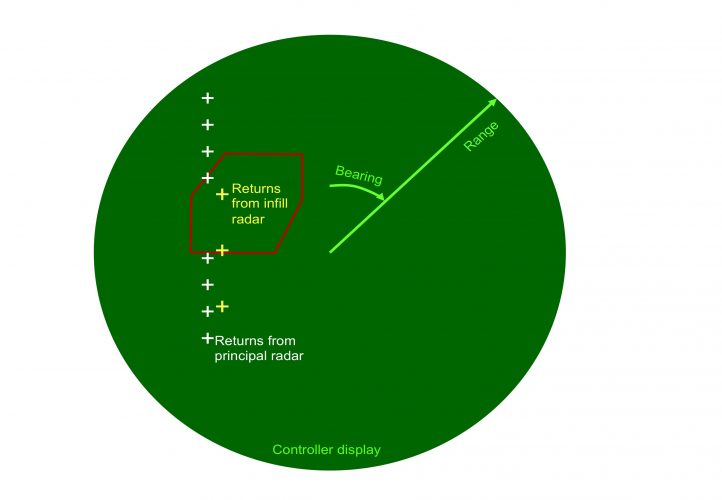
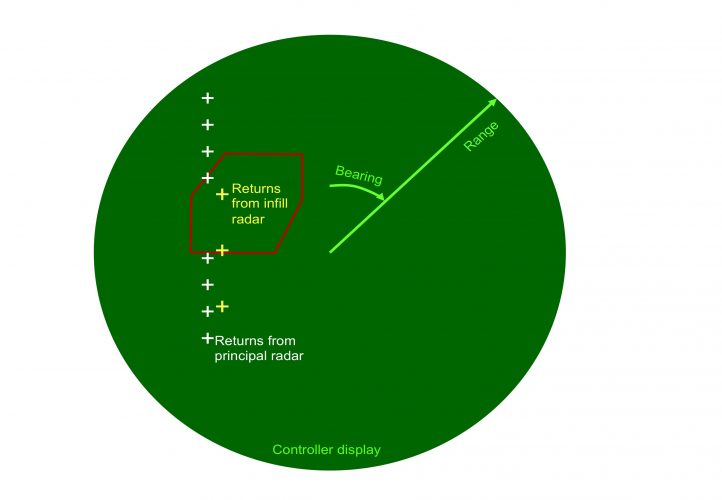
Figure 5: Infill mosaic display
For video-based radar displays this leads to a mix of video paints at different orientations to each other. While for plot displays, though the markers may remain the same, there will be time and position jumps as the target crosses a mosaic boundary. This is because the infill radar’s rotation is unlikely to be synchronised with the principal radar and the target position measured by the infill cannot be made to align with the principal radar’s measurement without target height information, which is not available to a 2D ATC radar. Thus mosaic integration of infill radar does not provide a seamless solution.
However, the main limitation of infill is that it requires external equipment fits on remote sites that need planning permission and spectrum licensing to build, complex safety cases to satisfy and resources to secure and maintain. Therefore achieving an aviation safety case for such a solution is not a trivial task, and in particular robust procedures need to be put in place by the ATS provider in the case of failure of the infill radar resulting in a large hole in radar coverage.
Nonetheless these risks are manageable and Whitelee’s infill mitigation solution has been operating since 2008.
Mini-infill
Mini-infill is a variation of the infill option using short range infill radars instead of full scale ATC radars.
The prototypes of mini-infill radars currently in development use finer Range, Azimuth or Doppler resolution than full-scale ATC radars to differentiate turbines from aircraft. Therefore, most mini-infill designs do not need terrain screening but allow the turbines to be visible to the mini-infill radar, which then passes only aircraft returns to the principal radar’s display. Several variants are expected to come to market over the next couple of years.
The low-level coverage of these systems is likely to be better than terrain-screened infills, however being short range they are not likely to be as good at high elevations. There is still the need to integrate the mini-infill data into the displays of the principal radar with the attendant integration issues described above. One potential mini-infill design does supply some 3D information to overcome the display alignment issue.
The main drawbacks of mini-infill radar are their short range and thus ability to mitigate only a small number of wind farms and the necessity to procure new land on which to site the mini-infill. For areas where wind farms proliferate, it is conceivable that multiple miniinfill radars would be required. Along with supporting and maintaining remote radars, this brings the issues of gaining planning permission, spectrum licenses, remote secured communication links and remote security.
It is because of this complex fragmented coverage display output that would result from failure of a mini-infill or communications links and the novelty of introducing such mini-infill equipment into aviation use that achieving a robust safety case may be quite challenging. It is thus unlikely that an ATS provider would accept multiple mini-infill radars.
However, for certain projects and ATS providers, mini-infill radars could provide a cheaper mitigation option and better performance than terrain screened infill.
Multi radar tracking
In the context of aviation radars, Multi Radar Tracking (MRT) is a means of integrating data from multiple radar sources into a single recognised air picture. It is a technology often employed in military air defence and increasingly in civil aviation. It is typically used when controllers need to monitor a sufficiently large volume of airspace that a number of radars are required.
An MRT system takes detection time and position measurements from various radar sources, associates them with aircraft targets and calculates the most likely position to display. This has the advantage that random and systematic errors are accounted for, displayed target position is more accurate than that derived from a single source and boundary crossings between radar coverage areas are smoothed.
In the UK, NATS maintains a network of long-range radars with overlapping coverage in order to provide en-route ATS, as well as accepting feeds from a number of airfield radars. Data from these radars is fed into NATS’ MRT systems to produce integrated air pictures at the company’s control centres in Swanwick (southern UK) and Prestwick (northern UK).
This overlapping cover and the presence of an existing MRT system has raised wind farm mitigation opportunities where some wind farms may be screened by terrain from certain NATS radars, which, provided they give sufficient cover overhead the wind farms, can provide infill for other NATS radars affected by the wind farms. Since this system already integrates radar data, there is no need for add-on mosaic display equipment, the only step necessary is to blank the wind farms in question from the affected radar feeds.
Taking advantage of this has enabled NATS to allow a large number of wind energy projects, many of which are now operational or under construction, particularly in Central Southern Scotland2. MRT is thus a successful mitigation option but one that does require a number of radars with conveniently overlapping cover. It is possible to add radars to such a network and NATS have already integrated some non en-route radars for the purposes of wind farm mitigation.
However, the number of allowable infills along with the size, and distribution of blanked areas is limited by the complexity of coverage (with a lot of gaps) that would result from particular failure modes.
Stealthy turbine blades
An approach being pursued by one turbine manufacturer is the integration of radar absorbent (stealthy) materials into turbine blades. This is not a trivial task since the blades must maintain their strength, flexibility and aerodynamic efficiency along with minimising any increased complexity or expense of manufacture.
A prototype ‘stealthy’ blade has been tested on a full size test turbine and has been found to have significantly reduced RCS when compared to a conventional blade. However, since turbine blades have very large RCS to start with, this still leaves stealthy blades with an RCS comparable to small aircraft and thus still capable of producing unwanted returns on radar displays. Nevertheless, the application of a stealthy blade would reduce the desensitisation impact on a radar system and may make other mitigation easier to achieve.
The main limitation to the deployment of stealthy blades is likely to be cost, since, for this option to be effective, every blade in a wind farm would need to be stealthy. For projects with tens or hundreds of turbines, each needing three blades, this could considerably increase the cost of the overall project.
Wind farm resilient PSR
Far and away the best approach is to address the problem directly and build mitigation into the primary surveillance radar’s design. By addressing the issues in each part of the radar system, new designs should be able to manage wind farm clutter much more effectively whilst maintaining good detection performance against aircraft targets.
Because almost every element of a radar system may be vulnerable to wind turbine effects, it is necessary to look at these design aspects from signal generation and receivers at the front end through the whole signal processing chain to plot and track extraction at the back end of the system3.
This approach has only become practical in recent years with the availability of large dynamic range components to eliminate the possibility of saturation or limiting and high performance signal processing hardware capable of applying sophisticated and sometimes intensive wind farm mitigating signal processing algorithms.
At BAE Systems, we have developed the Watchman Update, designed specifically to address the wind farm issue. Results from recent trials indicate that it is effective against both on- and offshore wind farms, eliminating wind turbine false alarms and maintaining very high detection performance against aircraft. In the meantime, while not specifically designed to mitigate wind farms, some other recent radar designs do appear to have somewhat improved resilience to wind farms as a result of incorporating new technology. NATS are also currently evaluating a wind farm specific mitigation suite from their radar supplier for application to their fleet of radars.
The key advantages of mitigating the primary radar is that the mitigation is applicable to wind farms anywhere within the radar’s coverage area, is self-contained on site, interfaces to existing equipment and infrastructure can remain the same and the mitigation has no impact on other systems apart from improved performance. This makes achieving an aviation safety case and maintaining such a system much simpler.
Conclusions
Wind turbines are a mature renewable technology and, with increasing pressure in governments to reduce carbon generation, it is likely that more wind farms will be built. However, wind turbines, can cause clutter, desensitisation and tracking problems for ATC radar. ATS providers thus take a conservative view on wind farm deployment and often end up in conflict with wind farm developers.
This approach is not sustainable and credible mitigation options are needed to allow wind farms and radars to co-exist. A variety of approaches to wind farm mitigation have been explored over the past few years, some of which have been operationally deployed. These all have certain benefits and certain drawbacks – most commonly more complex display integration and safety cases.
It has only been relatively recently that the technology has become available to enable the problem to be tackled within the ATC radars themselves and this seems to be the obvious and preferable solution. Aviation stakeholders have always attempted to constructively engage with wind farm developers but often have not had the mitigation options available to them to allow progress beyond deadlock, but with the emergence of these new options, the problems can now be reduced to manageable proportions, and aviation stakeholders along with wind farm developers are beginning to move forward together.
Further reading
- CAP 764: CAA Policy and Guidelines on Wind Turbines. www.caa.co.uk/cap764
- Eurocontrol Guidelines on How to Assess the Potential Impact of Wind Turbines on Surveillance Sensors. www.eurocontrol.int/documents/wind-turbines
- RenewableUK, Aviation & Radar. www.renewableuk.com/en/our-work/aviation-and-radar/
References
- C.A. Jackson, Windfarm characteristics and their effect on radar systems, Proc. International Conference on Radar Systems, Edinburgh, October 2007
- SW Scotland Regional Aviation Solution Group – Radar Feasibility Report – February 2010. www.scotland.gov.uk/ Topics/Business-Industry/Energy/Infrastructure/Energy- Consents/Guidance/Radar-Report
- C.A. Jackson and M.M. Butler, Options for mitigation of the effects of windfarms on radar systems, Proc. International Conference on Radar Systems, Edinburgh, October 2007
Biography
Clive A. Jackson PhD has been BAE Systems’ Wind Farm Technical Authority since 2006. He began his career in radar systems with BAE Systems in 2000 and has worked on many defence radar projects. Clive has developed mitigation strategies for many major wind farms and authored definitive studies on the subject. As a result of developing robust radar mitigation strategies he has helped achieve planning consent for over 800MW of wind power, corresponding to over £2 billion of investments. Clive can be contacted by email at: [email protected]