Can F3 agents take the fire security heat?
Posted: 17 November 2016 | Mike Willson (Fire Protection Consultant) | No comments yet
Fire protection consultant, Mike Willson, provides in-depth analysis of a recent foam seminar that examined this point…
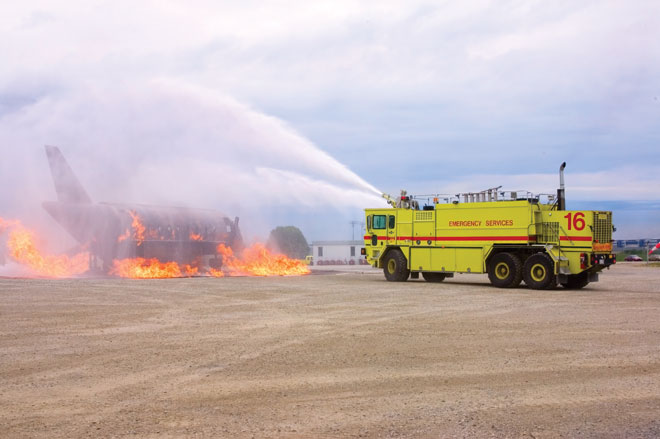
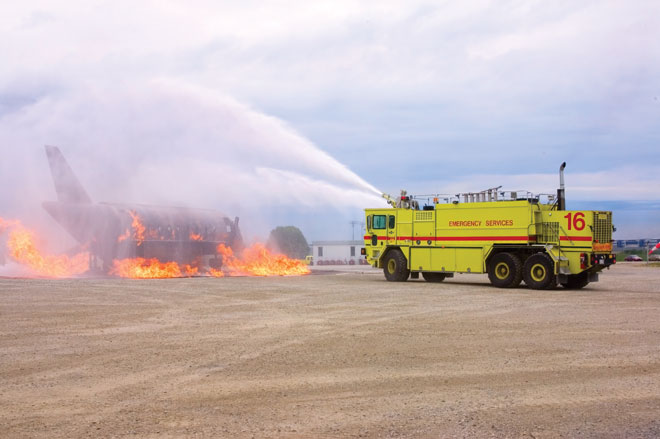
We are seeing a transition occurring in aviation from long-chain C8 fluorinated AFFFs (aqueous film forming foam) towards short chain C6 fluorosurfactant-based AFFFs and alternative fluorine free foams (F3). These C6 retain the essential fuel shedding and fire security capabilities of the historically used longer-chain agents. Fire protection consultant, Mike Willson, provides in-depth analysis of a recent foam seminar that examined this point.
A recent foam seminar in Singapore examined this question, showcasing research and a planned F3 fire demonstration. Entitled ‘The Future of Firefighting Foams: Minimising its Environmental Impact for Greater Sustainability’ and jointly organised by the Singapore Aviation Academy and the International Aviation Fire Protection Association, this major Asian seminar had 80+ preeminent speakers and delegates attending worldwide. The views expressed are the author’s and not the organisers of this Singapore conference. However it is intended to be a fair representation of events. Educational and generic discussion was provided to help end users understand and decipher often conflicting claims, promises and regulations concerning firefighting foams. Interestingly, all the foam manufacturers represented produce both F3 and C6 fluorinated foams.
The seminar covered wide-ranging topics, from practical firefighting experiences; new research; regulatory changes; aquatic toxicity and remediation and transitioning alternatives; to existing longchain C8 fluorinated foams that are currently much in use, and lots more. The following are a few highlights.
Much debate revolved around these complex issues:
- F3 technology is sufficiently advanced to replace fluorinated foams
- Short-chain C6 technology is necessary to provide safety, reliability and effectiveness; critical to prevent major fire hazards from delayed control, escalation and life exposure
- Current emphasis on environmental impacts of foam concentrates has an overbearing and potentially over-precautionary role
- Recognising overall incident environmental impacts as a complete event, may give different answers.
Many believe the environmental impact of foam cannot be divorced from those of major incidents, where effects of noxious smoke, toxic and often carcinogenic breakdown products enter firewater run-off and personal protective equipment (PPE). Limiting generation of these noxious substances may hold the key to minimising the environmental impacts of such events.
Changi Airport’s Fire Chief, Cletus Packiam, welcomed delegates with an insight into the airport’s professionalism and swift response to a recent airliner engine fire on landing; extinguished after 2.5 minutes using AFFF and film-forming fluoroprotein (FFFP). All passengers were rescued safely, without injury. Some delegates questioned whether it would have been the same story if F3 had been used?
Aditya Parekh, from Firechem in India, referenced the first transPacific solar-powered flight without using fossil fuels. Future aviation hazards are changing, requiring a paradigm shift in our thinking and technology. Meanwhile, pollution created by fire should be balanced against pollution caused by firefighting, while recognising that speed and performance minimise environmental impacts. Every second counts toward saving a life.
We learned of several important incidents where AFFF and F3 agents were used:
- 1967 USS Forrestal tragedy: 134 lives lost, 62 injured and 21 aircraft destroyed. This incident employed the first generation of fluorine free protein foam and encouraged development of AFFFs and subsequently the U.S. Mil-F-specification – the world’s toughest foam specification, used by civil and military aviation throughout USA
- 2013 Asiana Airlines crash in San Francisco: 307 passengers on board, 187 injured and only three died. Evacuation started 90 seconds after impact. MilSpec AFFF foam rapidly extinguished fuselage fires, preventing escalation so that casualties could be safely rescued. Some delegates asked whether this would have been possible with F3 agents
- 2013 Caltex Banksmeadow, Sydney incident: here, F3 agent lasted only 15-20 minutes between top-ups on an unignited gasoline spill. Fluoroprotein foam lasted 4.5 times longer at 90 minutes between top-ups, while still retaining adequate vapour control
- 2013 ‘Simulated storage tank fire with fuel in depth’ in Beaumont, Texas: The calculated fuel depth was only 1.33cm – a spill fire inside a tank shell – requiring an F3 application rate of 10.3L/min/m2 to extinguish, when NFPA 11 calls for just 4.1 l/min/m2 ; almost three times more.
Demonstration F3 fire test replaced
Solberg’s demonstration fire test by Luc Jacobs, Jan Solberg and James Perriss was intended to showcase the company’s leading F3 on an ICAO Level B fire, but unfortunately it had to be replaced by C6 AFFF. Luc explained: “We demonstrated C6 AFFF as too many environmental factors were not under our control to do F3.” Several delegates protested that “those variables usually happen during fire incidents”. It was disappointing as, while a demonstration can be cancelled, real emergencies cannot.
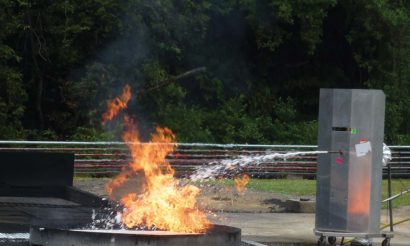
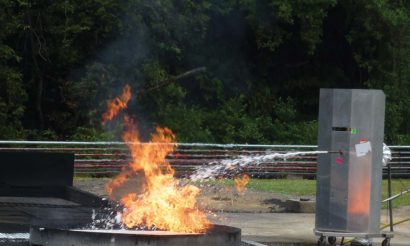
Figure 1 shows the 3% C6 AFFF effectively providing control and extinction, without edge flickers, despite humid 32°C conditions. Allegedly this same fire was unable to be extinguished twice using F3 the day before, and even caught the separator alight. Several delegates had not appreciated that fuel volatility usually increases with increasing ambient temperatures, while foam quality usually decreases; making fires harder to extinguish.
Some delegates had anticipated movement to F3 for environ mental reasons and were visibly disappointed at not being able to witness first-hand the ICAO Level B performance of an F3 foam.
Author’s note: Such fire tests are usually conducted at 15-20°C to enable comparison. Although you can argue that the safety margin should be adequate, recommended application rates usually double test rates and many variables including temperature, long pre-burns, wind/rain effects, hot metals, obstructions, faulty equipment, foam blanket interruption, training shortfalls and many more demands are placed on this safety margin.
Prior to the lunch break on Day One, Changi Airport’s Lin Yew Swee reminded us that the Airport Services Manual (Doc 9137)1 requires that: “…foam must flow freely over the fuel surface, must resist disruption due to wind or exposure to heat or flame and should be capable of resealing any rupture caused by disturbance of an established foam blanket.” Delegates asked whether modern C6 and F3 agents meet these criteria? Aviation foams must deliver quick knockdown as “seconds can mean the difference between life and death. The risk of fire burning back again is a serious trap for passengers and firefighters – resisting re-ignition is critical”.
Author’s note: The cancelled F3 demonstration reinforces our duty of care to passengers’ and firefighters’ lives; confirming challenging test conditions better represents the day a fire strikes. Foam without fluorine doesn’t mean ‘no problems’ as some regulators seem to believe. There are no substitutes for appropriate firefighting performance, as every second counts towards saving lives.
Need for transition
I suggested that transitioning away from long chain ≥ C8 PFOS and PFOA foams is necessary to achieve more environmentally-responsible outcomes, but with which alternatives – F3s or short-chain ≤ C6 foams? I reviewed current public concerns over PFOS/PFOA, highlighting substantial differences of C6 fluorosurfactants which are Persistent (P), but neither Bioaccumulative (B) nor Toxic (T), with human half-life averaging 32 days for PFHxA2 . This compares with the findings for PFOS/PFOA – both PBT substances with human half-lives averaging 5.4 and 3.5 years respectively3 . C6 AFFFs are already recognised and accepted by the U.S. EPA, European Chemicals Agency, UK Environment Agency and NICNAS for use in Australia.
Author’s note: Regulators are setting ever-lower threshold acceptance levels. The U.S. EPA reduced drinking water requirements to 70 parts per trillion (ppt) for PFOS/PFOA combined4 . Germany’s Environment Agency has set no adverse effect human blood levels of 5ng/L PFOS, 2ng/L PFOA5 . For context, 1ng/L =1ppt = 0.001ppb. 1ppt equates to three seconds in 100,000 years6 ! Scientists are investigating the implications of these restrictions, when typically developed populations already have 7,000-24,000ppt of PFOS/PFOA in their blood7 . We questioned whether anyone is being harmed or is this over-precautionary?
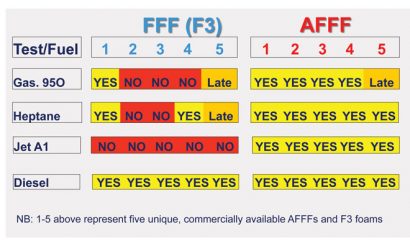
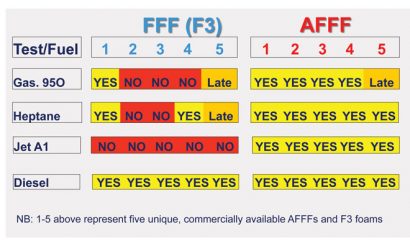
Figure 2: Fire test extinguishment results: Fluorine free vs. AFFF
Controversy was caused by some of Luc Jacobs’ Solberg slides under the heading ‘Myths and Facts’. A fact suggesting that four times more 99.5% purity C6 was needed to equate to existing C8 AFFF agents, was dismissed by other presentations showing equivalency of C6:C8 in two separate AFFF agents, both of which successfully passed all MilSpec tests.
Author’s note: Claiming ‘myth’, the suggestion that F3s do not generally perform as well as AFFFs, had ignored established research concluding “best-performing FfreeF formulation (RF6) provides about 30% of the durability of an AFFF for protection against evaporation of low-flashpoint flammable liquids8 ”. This was also substantiated by the Caltex unignited gasoline incident above.
Exciting and comprehensive new research undertaken by Javier Castro of Auxquimia, Spain evaluated 80+ comparative fire tests between F3 and C6 foams to help resolve the “tug of war” between firefighting performance and environmental impacts. Five ARAFFFs (1, 3 and 4 are ≤ C6 fluorotelomer surfactant-based, with 2 and 5 being ≥ C8 fluorinated) and five fluorine free AR-F3s were tested on four hydrocarbon fuels at three different application rates, under uniform test conditions, mirroring results achieved at EN1568 and ICAO Level B.
Averaged control times showed AR-F3 60% slower on Gasoline (G95) and 50% slower on Jet A1 than AR-AFFFs. Significant weaknesses were confirmed by this 2.5L/min/m2 summary in Figure 2.
Further testing showed control times on Gasoline and Jet A1 were 100% slower for AR-F3 compared to AR-AFFF at 1.25L/min/m2 , yet on Heptane both were around 50% slower. Differences narrowed at higher application rates, with AR-F3 typically 10% slower (Jet A1), 25% slower (Gasoline) and 50% slower (Heptane), than the AR-AFFF results. F3s can also take 80 seconds to achieve control of spill fires, yet film formation allows AFFFs to reduce this to 30 seconds – almost three times less. AR-AFFFs provided faster fire control, superior fuel repellency, greater effectiveness and versatility on a wider range of fuels and conditions. Substantial differences on Jet A1 were particularly striking due to its critical ARFF use (Figure 3).


Figure 3: Dynax summary slide, from SAA-IAFPA Fire-fighting Foam Seminar
Dr Chang Jho confirmed Dynax research also highlighted that fuel contamination is a serious yet unavoidable problem for F3, causing edge flickers, increased flammability and premature foam breakdown9 . Key firefighting advantages to protect life, our environment and property were compared. Adding just 0.042% C6 fluorosurfactant to F3 prevented both ignition and sustained burnbacks. 2015 U.S. Naval Research Laboratories (NRL) found “AFFF had a much longer foam lifetime than fluorine free RF6; when exposed to n-heptane fluorination appears to reduce degradation10”. Also observing: “RF6 foam lifetime changing from one hour on water to three minutes on n-heptane degradation [compared to AFFF lasting 35 minutes on n-heptane], seen during extinction may be caused by fuel and not pool temperature.” This demonstrated fundamentally undesirable issues with F3 foams, which could occur in real fire situations. Chang suggested in closing that alternative ways to compensate for some of these fundamental weaknesses could include using significantly more volume (typically up to three times more F3), or choosing gentle application methods.
During my own presentation I brought to the delegate’s attention the fact that evidence suggests firewater runoff is the real demon. It often contains Polycyclic Aromatic Hydrocarbons (PAHs) and other toxic breakdown products including hydrogen cyanide – some of which are known carcinogens and probably attributable to increased incidence of cancers in firefighters11,12. Studies of 224,000 Australian firefighters showed 79% of fires attended by career, paid part-time and volunteer firefighters were structural, vehicle and bushfires12 not requiring Class B foams. Queensland research shows fire breakdown products can enter the skin under/through PPE, and by inhalation during incidents, overhauls and transfers back to station11, with exposures potentially contributing to a significant increase in prostate cancer found in firefighters12. Recommendations included showering and clothing changes on fire-ground, with container-sealing PPE to avoid off-gassing and laundering regularly11.
“Achieving more with less by swiftly controlling and extinguishing the fire, releasing less breakdown products and producing less firewater runoff, reduces the potential to cause environmental harm when all foams and runoff pollutes…”
David Plant from Angus International in the UK asked ‘what firefighting foam is sustainable?’ Using 2014 UK Environment Agency’s advice: “Fire service foam buyers’ primary concern should be which foam is the most effective at putting out the fire. All firewater runoff and all foams present a pollution hazard13.” This approach ensures life safety, limits escalation, reduces foam and runoff volumes, and minimises subsequent pollution.
Most delegates seemed unaware that C6 fluorosurfactants account for <2% of fluorinated foam concentrates, further diluted 100 times for use strength. “The introduction of fluoro-surfactants into firefighting foams was one of the most important innovations in the past century for the rapid control and extinguishment of flammable liquid fires,” confirmed important 2005 research14. Why relinquish its benefits?
An independent 2014 study by Eurofins Laboratoire Toxlab in France conducted for Angus Fire15 compared aquatic toxicity for different foam types required to kill 50% of test fish species over a 96 hour period. Incredible variations occurred from just 38-110 ppm for F3 agents (most toxic) to 5,100ppm for AFFFs (less toxic); a staggering 134 times less toxic than the worst F3 tested. The importance of such toxicity was demonstrated by river pollution impacts following a major UK chemical incident where firefighting foam and runoff escaped and killed 20,000 fish, which took six years before forced re-stocking with 24,000 fish, as they did not return naturally. An indication, perhaps, that ecosystems don’t normally “bounce back” from severe toxicity events, as some claim when using more toxic F3 agents.
On Day Three Brian McKinney, Fire Chief Dallas/Fort-Worth International Airport, summ – arised the future of AFFF in the USA, confirming MilSpec AFFFs rapidly extinguished two major aircraft fires. He also reminded us that all U.S. airports are required by FAA to use only MilSpec QPD AFFFs, which is the toughest fire specification in the world and essential at U.S. airports, yet F3 agents fail to meet it. The value of live jet fuel training was also highlighted, as flammable pools can’t be switched off like gas props, and can easily relight with F3 training foams, delivering more life-like scenarios.
Former Fire and Security Advisor at Petrochemicals in Singapore, Mr Hong Kim Pong, shared 40 years of expertise by providing important hints and tips, reinforcing that fully developed fires may reach ≥ 500°C. Intense heat causes flange/seal failures, jet fires and structural collapses, often delivering a ‘domino effect’ of conse – quences, potentially leading to huge fuel releases and/or explosions. Successful extinguishment relies on reliable foams and equipment, plus process safety management systems and realistic well-practiced emergency plans, delivered by well-trained, experienced firefighters.
Rounding off the seminar, Lastfire Group’s Dr Niall Ramsden considered what the future may hold in terms of potential legislation, increasing concerns, controls, restrictions and developments. He said we should expect a “cradle to grave” approach with increased containment/remediation/disposal focus, without losing sight of benefits in a risk-based approach to deliver reliable fire control. Systems assurance, novel equipment solutions with developing foam assurance protocols and self-audit/third party assessments, could be applicable to a wide range of applications. “Don’t rush to change” was the message – understanding realistic and practically safe guidelines to protect human health, in context of the multiple societal benefits these agents provide, are critical in order to secure a safe future.
Conclusions
Delegates found the seminar worthwhile, thought provoking and engaging: from fundamental principles of foam and fuel interactions, to dealing with key issues facing firefighters and end users today. Useful views on moving forward were shared, with structures and suggested processes to help guide and keep us safe, in a more restrictive regulatory environ ment. Achieving more with less by swiftly controlling and extinguishing the fire, releasing less breakdown products and producing less firewater runoff, reduces the potential to cause environmental harm when all foams and run-off pollutes. Most concluded that decisions cannot be made on environmental profiles alone. Many factors need consideration, and each must weigh up what works best to meet their specific site needs.
Everyone appreciated the high level of welcome and conference support from our hosts and sponsors, making this such a valuable event – the template of which can be widely replicated. Feedback showed high levels of satisfaction with all aspects of the conference; 82% acquiring new knowledge, resolving confusions and seeing things differently as a result of participation.
Mike Willson has over 25 years’ experience in the fire industry across all sectors involving flammable liquids. He has technical specialist knowledge on Class B firefighting foams, their differences, application, fire performance and environmental impacts of all foam types. Mike currently works as a consultant, providing technical assistance and advice to a diverse range of stakeholders, primarily regarding regulatory positions on firefighting foams at facility, state, federal and international level. He attempts to achieve less blinkered, more balanced and practical outcomes to benefit our environment, regulators and foam users, and potential incident casualties.
References
- ICAO (international Civil Aviation Organization), 2014 – Airport Service Manual Doc 9137, Part 1 AN/898 Chapter 8 Rescue and Fire Fighting 4th Edition, https://www.bazl.admin.ch/ …/ICAO/icao_doc_9137_airportservicesmanualpart1withn…
- Russell, Nilsson, Buck, 2013 – Elimination Kinetics of PerFlouroHexanoic Acid in Humans and comparison with mouse, rat and monkey, Chemosphere, Sep2013 ISSN 1879-1298 http://www.biomedsearch.com/nih/Elimination-kinetics-perfluorohexanoic-acidin/24050716.html
- Olsen G et al – Evaluation of the Half-life (T1/2) of Elimination of Perfluorooctanesulfonate (PFOS), Perfluorohexanesulfonate (PFHxS) and Perfluorooctanoate (PFOA) from Human Serum, 2007. http://www.chem.utoronto.ca/symposium/fluoros/pdfs/TOX017Olsen.pdf
- US EPA, 2016 – PFOA and PFOS Drinking Water Health Advisories – Factsheet https://www.epa.gov/sites/production/files/2016- 05/documents/drinkingwaterhealthadvisories_pfoa_pfos_5_19_16.final_.1.pdf
- Umwelt Bundes Amt (UBA), 2016 – Reference and HBM Values https://www.umweltbund esamt.de/en/topics/health/commissions-working-groups/human-biomonitoringcommission/reference-hbm-values
- Wikipedia 2016 – Parts per Notation https://en.wikipedia.org/wiki/Parts-per_notation
- Toms, Rotander et al, 2011 – Decline in PFOS & PFOA serum concentrations in an Australian population 2002-2011 http://eprints.qut.edu.au/78642/
- Schaefer T, et al, 2008 – Sealability Properties of Fluorine-Free Firefighting Foams, University of Newcastle, Australia, Fire Technology Vol 44.issue 3 pp297-309 http://novaprdlb.newcastle.edu.au:8080/vital/access/manager/Repository/uon:4815;jsessionid=E0140D58 6B0467E75B68993EBC83A1CA?exact=sm_subject%3A%22vapour+suppression%22
- Jho C, 2012 – “Flammability and degradation of fuel contaminated fluorine-free foams”, International Fire Fighter, Dec 2012, MDM publishing. http://www.dynaxcorp.com/ resources/pdf/articles/Flammability-IFF.pdf
- Hinnant K et al, 2015 – “Evaluating the Difference in Foam Degradation between Fluorinated and Fluorine-free foams for Improved Pool Fire Suppression,” US NRL, ARL-TARDEC Fire Protection Information Exchange Meeting, Aberdeen Proving Ground, MD, October 14, 2015
- Kirk K and Logan M, 2015 – Structural firefighting ensembles – accumulation and off-gassing of combustion products, Journal of Occupational and Environmental Hygiene, DOI: 10.1080/15459624.2015.1006638
- Sim M and Glass D, 2014 – Final Report Australian Firefighters’ Health Study, Monash University Centre for Occupational and Environmental Health, Dec.2014 http://www.coeh.monash.org/downloads/finalreport2014.pdf
- Gable M, 2014 – “Firefighting foams: fluorine vs non-fluorine”, UK Environment Agency, Fire Times, Aug-Sep 2014.
- Dlugogorski et al, 2005 – Dynamic surface and interfacial tension of AFFF and Fluorine Free Class B Foam Solutions, University of Newcastle , Australia
- Eurofins Laboratoire Toxlab, 2014 – Compilation of 27 aquatic toxicity test reports conducted by Eurofins Laboratoire Toxlab in Paris, France for Angus Fire during 2014.
New report from International Airport Review: Securing Airports in an Evolving Threat Landscape
International Airport Review has brought together top voices from across the global aviation security sector, including International Civil Aviation Organization (ICAO), ACI World, Fraport, Qatar Civil Aviation Authority, Winnipeg Airports Authority, and Smiths Detection to examine today’s most pressing airport security challenges and emerging threats.
This expert-led report provides a strategic assessment of the vulnerabilities facing airports in 2025, encompassing cyber-attacks, drone incursions, evolving geopolitical risks, and emerging technologies.
The result is a practical, insightful guide to strengthening airport resilience, anticipating risks before they escalate, and keeping your airport off the front page
Download the report for free and stay ahead of the security curve – READ FOR FREE NOW!